A Comprehensive Guide to Inventory Control: Definitions and Methods Explained
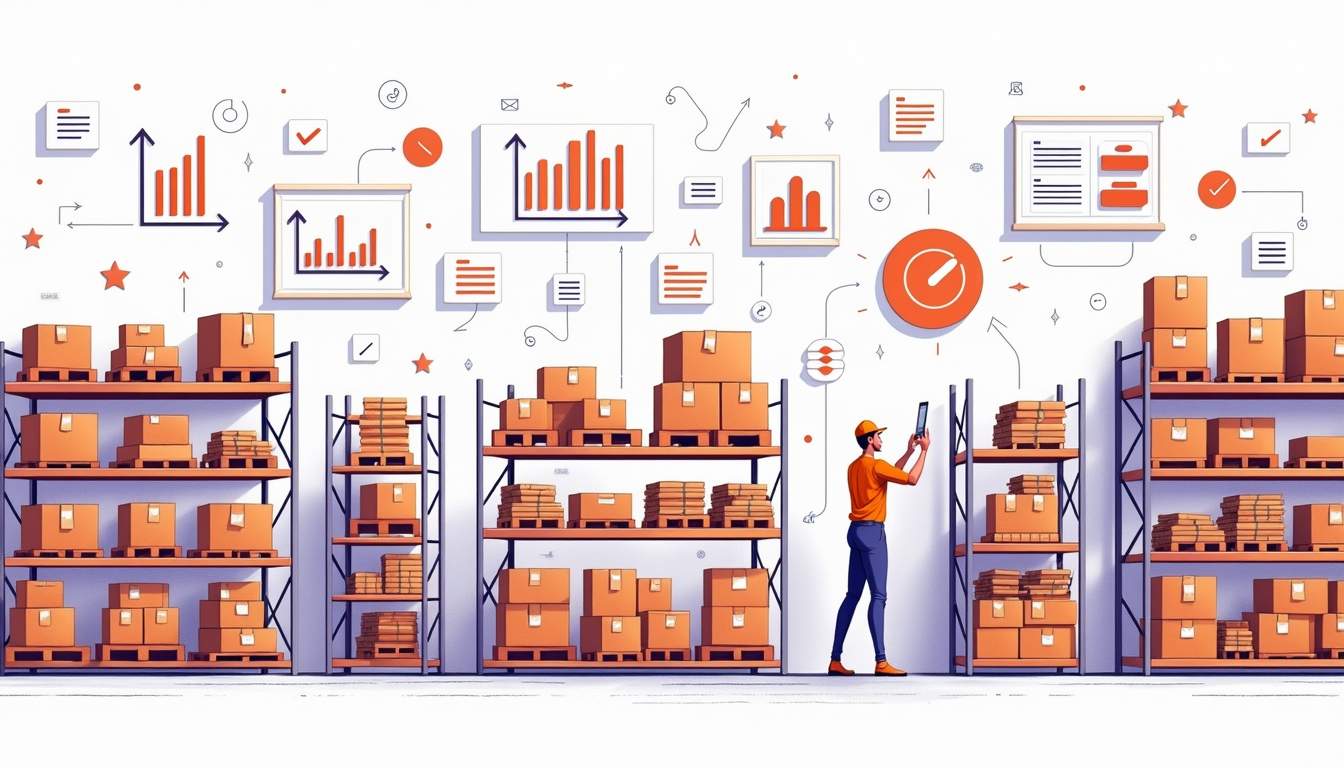
In today's fast-paced business environment, managing inventory efficiently is crucial for maintaining profitability and meeting customer demands. This article dives deep into the essential aspects of inventory control, offering insights and strategies for effective management.
Understanding Inventory Control: An Overview
Inventory control involves overseeing and managing stock levels, orders, and inventory storage. It enables businesses to have the right products available at the right time while minimizing carrying costs. In simpler terms, effective inventory control ensures that there is neither excess inventory tying up cash flow nor stockouts leading to missed sales opportunities.
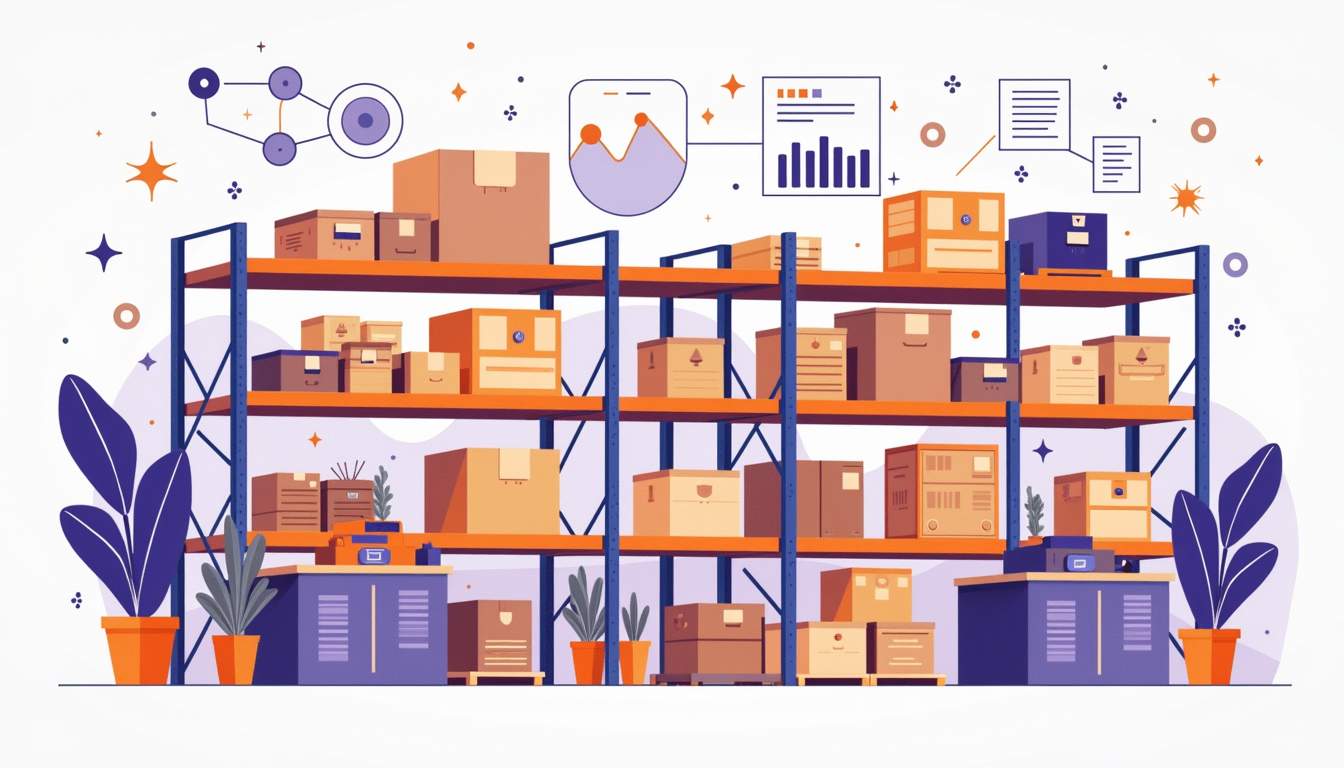
Several factors can influence inventory control, including supply chain efficiencies, market demand trends, and seasonal fluctuations. A robust inventory control system is essential for operational success, especially in industries like retail, manufacturing, and logistics.
One of the key components of effective inventory control is the implementation of technology-driven solutions. Modern businesses often utilize sophisticated inventory management software that provides real-time data on stock levels, sales trends, and supplier performance. These systems can automate reordering processes and generate alerts when stock levels fall below predetermined thresholds, thereby reducing the risk of human error and ensuring timely replenishment. Furthermore, integrating inventory management with other business systems, such as accounting and customer relationship management (CRM), can enhance overall operational efficiency and provide a holistic view of business performance.
Additionally, understanding the different inventory valuation methods—such as FIFO (First In, First Out), LIFO (Last In, First Out), and weighted average—can significantly impact financial reporting and tax obligations. Companies must choose the method that aligns best with their operational strategy and market conditions. For instance, FIFO is often favored in industries with perishable goods, as it helps minimize waste and ensures that older stock is sold first. In contrast, LIFO may be advantageous during periods of rising prices, allowing businesses to reduce taxable income. Ultimately, a well-rounded approach to inventory control not only streamlines operations but also supports strategic decision-making and enhances customer satisfaction through improved product availability.
What is Inventory Control?
Inventory control can be defined as the process of managing a company's inventory to ensure that the correct quantity of products is in stock at all times. This process includes tracking, ordering, and managing products through various stages of production and sales channels.
Inventory control provides businesses with the ability to forecast demand, thereby ensuring they can meet customer expectations without incurring unnecessary costs. By maintaining optimal stock levels, businesses can also reduce the risk of spoilage or obsolescence, particularly in sectors with perishable goods or rapidly evolving technology.
Effective inventory control systems often utilize advanced technologies such as barcode scanning, RFID (Radio Frequency Identification), and inventory management software. These tools not only streamline the tracking process but also enhance accuracy in stock counts, which is crucial for making informed purchasing decisions. For instance, a retail store equipped with a robust inventory management system can quickly identify which items are selling well and which are not, allowing for timely restocking or clearance sales to optimize inventory turnover.
Moreover, inventory control is not just about maintaining stock levels; it also involves strategic planning and analysis. Businesses can leverage historical sales data to identify trends and seasonal fluctuations, which can inform their purchasing strategies. For example, a company might increase its inventory of winter apparel in anticipation of colder months based on previous sales patterns. Additionally, effective inventory control can improve cash flow management, as it helps businesses avoid over-investing in stock that may not sell, thus freeing up capital for other operational needs.
Exploring Different Inventory Control Techniques
There are several techniques to manage inventory efficiently. Each method works differently depending on factors like the size of the business, industry requirements, and specific product types. Here are some prominent techniques widely used in inventory control.
The ABC Method of Inventory Management
The ABC method categorizes inventory into three groups: A, B, and C. Group A consists of high-value items that typically account for a significant portion of overall inventory cost but represent a smaller volume of products. Group B contains moderate-valued items with a balanced volume, while Group C includes low-value items that require less attention.
This classification allows businesses to prioritize their efforts and resources, ensuring that more significant resources are allocated to managing high-impact inventory. It effectively streamlines processes, improving efficiency and reducing costs with focused attention on high-value items. Additionally, the ABC method can be complemented by regular reviews and adjustments, allowing businesses to adapt to changing market conditions and product lifecycles. By periodically reassessing inventory classifications, companies can ensure that they remain agile and responsive to shifts in demand or supply chain disruptions.
Utilizing Visual Control for Inventory
Visual control refers to using visual aids to manage inventory levels and flow. Techniques such as color coding, charts, and diagrams can provide a quick reference for employees to assess stock positions at a glance. Visual cues can help improve accuracy in inventory tracking and reduce errors in order fulfillment.
By implementing visual control systems, companies can enhance communication and foster a collaborative environment, as all team members can easily understand stock levels. This method is particularly effective in warehousing and production settings, where a dynamic flow of goods is common. Furthermore, visual controls can be integrated with technology, such as inventory management software that includes dashboards and alerts, providing real-time insights into stock levels. This combination of visual and digital tools not only boosts operational efficiency but also empowers employees to take ownership of their roles in inventory management, leading to a more engaged workforce.
The Fixed Order Inventory Approach
The fixed order quantity method is characterized by ordering a predetermined quantity of inventory whenever stock levels fall below a specific threshold. This approach simplifies reordering processes and ensures that businesses don’t run out of essential items.
Using this approach often relies on historical data and lead time considerations. By calculating the optimal order quantity, businesses can avoid stockouts while keeping carrying costs manageable. This method is ideal for products with predictable demand and stable lead times. Moreover, businesses can enhance this technique by incorporating safety stock levels to buffer against unexpected demand spikes or supply chain delays. This additional layer of protection can be crucial for maintaining service levels and customer satisfaction, particularly in industries where timely delivery is paramount.
Understanding the Order Period Method
The order period method revolves around placing orders at fixed intervals rather than when stock levels reach a specific threshold. Companies maintain a consistent schedule for ordering inventory, which helps manage lead times effectively.
This strategy is particularly useful in environments with fluctuating demand, as it enables companies to anticipate trends and adjust their ordering schedules accordingly. The order period method also helps streamline inventory reviews and analysis, fostering a proactive approach to stock management. Additionally, businesses can benefit from integrating demand forecasting techniques into this method, allowing them to better predict future inventory needs based on historical sales data and market trends. This foresight not only minimizes excess inventory but also maximizes turnover rates, ultimately contributing to healthier profit margins.
Getting Started with Inventory Control
Implementing an effective inventory control system is a manageable process if you follow the right steps. Understanding your inventory, defining stock levels, and utilizing appropriate tools are essential. Let’s explore how to get started.
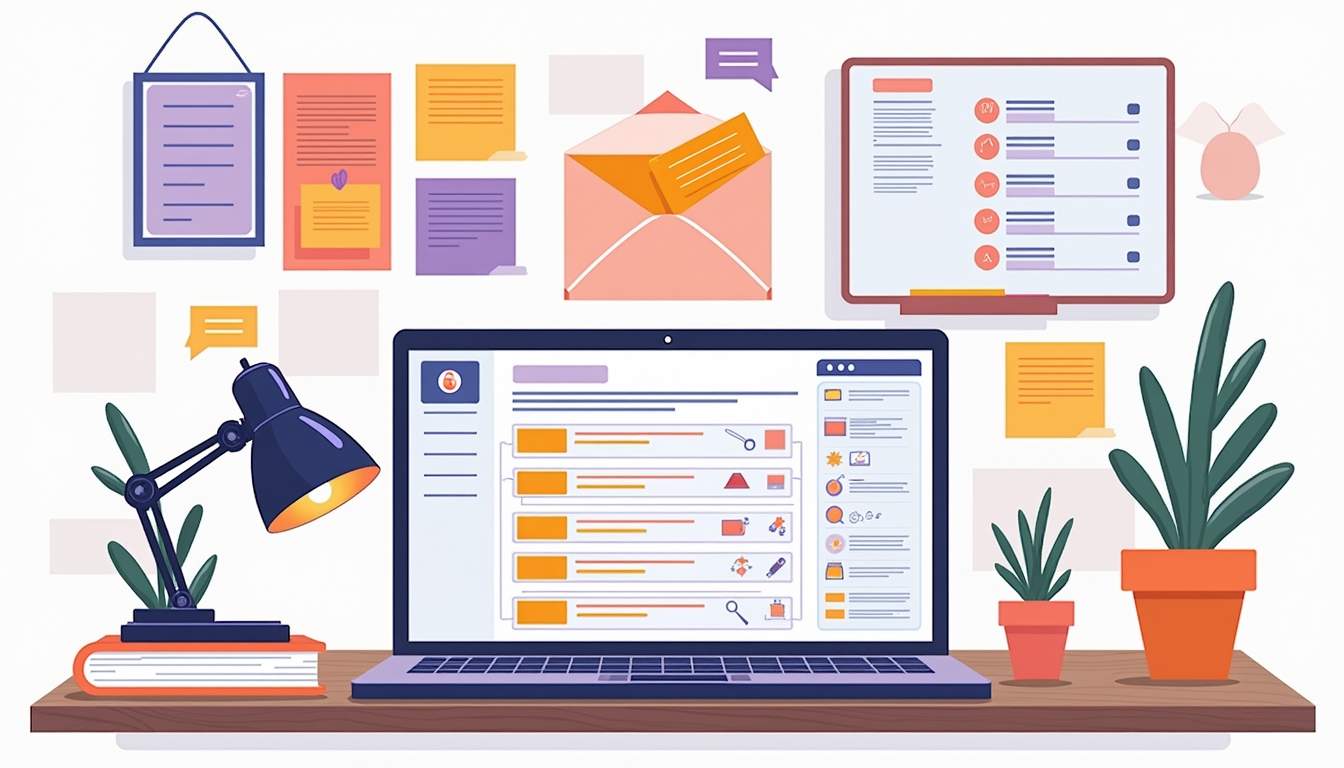
Generating SKU Numbers Using Excel Templates
Stock Keeping Units (SKUs) are essential for tracking inventory. Generating SKU numbers uniquely identifies each product, facilitating accurate tracking and analysis. Excel templates can simplify this process.
By using Excel, businesses can create easily customizable SKU formats that incorporate essential product details. These may include factors such as category, size, color, or model information. Automating SKU generation can save time and reduce errors associated with manual entry. Furthermore, integrating SKU numbers with inventory management software can enhance visibility and streamline operations, ensuring that all team members have access to up-to-date information.
Defining Optimum Stock Levels
Determining optimum stock levels is a critical aspect of inventory control. It involves analyzing demand patterns, lead times, and cost considerations to identify the ideal quantity to maintain for each item.
This evaluation helps prevent overstocking and stockouts. By employing forecasting techniques, businesses can accurately predict customer demand and adjust their stock levels accordingly. This ongoing assessment process helps maintain healthy inventory and ensures continual responsiveness to market changes. Additionally, using inventory management systems that incorporate real-time data can further refine stock level decisions, allowing businesses to react swiftly to unexpected shifts in demand or supply chain disruptions.
The Role of Batch Production in Manufacturing
Batch production is a manufacturing approach that produces goods in groups or batches rather than in a continuous flow. This method impacts inventory control directly, as it requires careful management of raw materials, work in progress, and finished goods.
When using batch production, it is crucial to ensure that inventory levels match production schedules to avoid delays. Properly aligning these aspects can help minimize wastage and maximize efficiency, particularly in scenarios where product demand fluctuates. Moreover, implementing just-in-time (JIT) principles can complement batch production by reducing the amount of inventory held at any given time, thereby lowering holding costs and enhancing cash flow.
Evaluating the Make to Stock Strategy: Pros and Cons
The make-to-stock strategy refers to producing goods based on anticipated demand, holding finished products in inventory until sold. This approach has its advantages and challenges. On the plus side, it allows businesses to fulfill customer orders quickly, improving service levels and customer satisfaction.
However, it can also lead to excess inventory if demand is miscalculated. Balancing stock levels with production can be tricky, requiring robust forecasting practices and market analysis. Businesses must weigh these pros and cons carefully when deciding on their manufacturing approach. Additionally, companies may consider implementing a hybrid model that combines make-to-stock with make-to-order strategies, allowing for greater flexibility and responsiveness to customer needs while minimizing the risks associated with overproduction.
Simplifying Selling Price Determination
Determining the right selling price is another critical component of inventory control. Prices should reflect both the cost of goods sold (COGS) and the market demand to ensure profitability while remaining competitive.
To simplify this process, businesses can utilize cost-plus pricing strategies, market research, and competitive analysis. Accurately understanding costs associated with inventory not only helps in setting prices but also contributes to effective inventory management decisions. Furthermore, leveraging technology such as pricing optimization software can provide insights into customer behavior and market trends, allowing businesses to adjust their pricing strategies dynamically and maximize revenue potential.
In conclusion, effective inventory control is a multi-faceted endeavor involving various strategies and techniques. By understanding the different methods available and their implications for your business, you can create a more streamlined approach, optimizing inventory management and promoting growth.