Clarifying the Differences Between Manufacturing and Production Processes
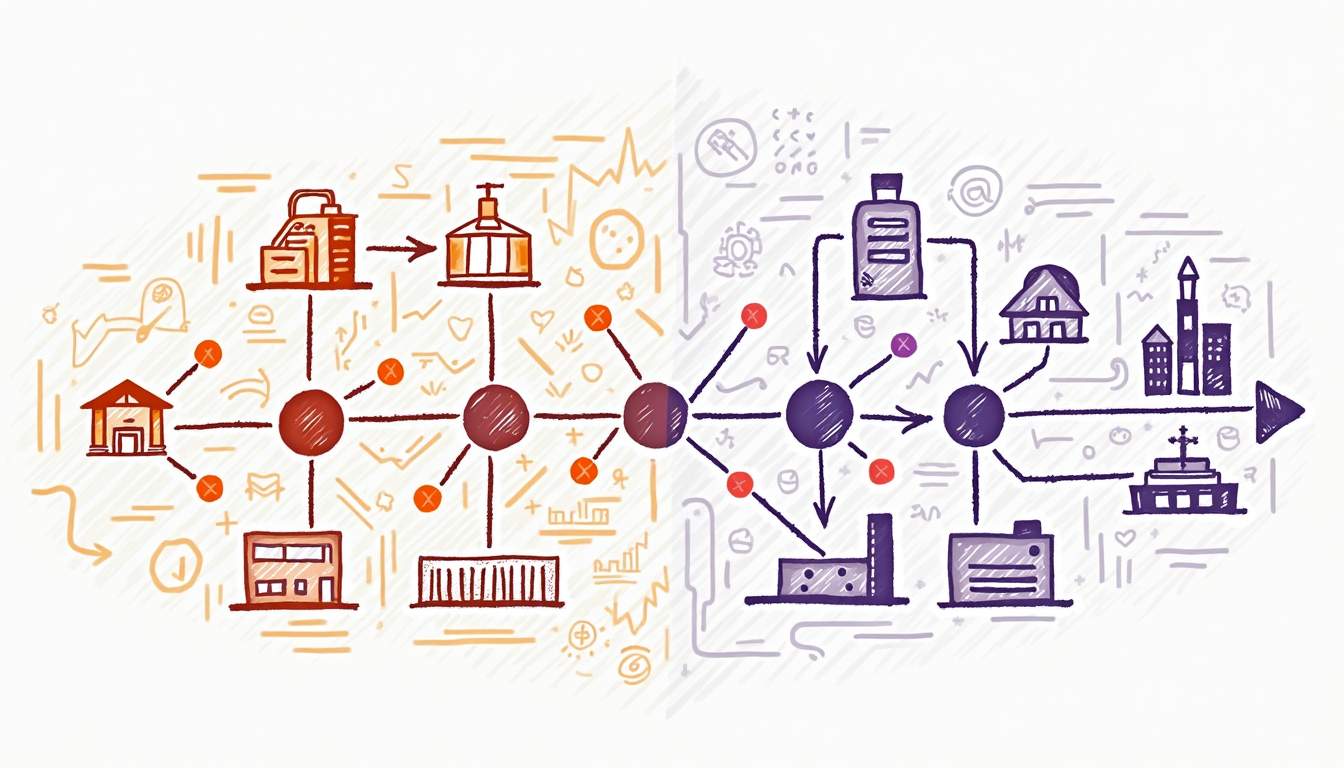
Understanding the intricate worlds of manufacturing and production is essential for anyone looking to delve deeper into the industry. These terms are often used interchangeably, but they encompass distinct processes that play crucial roles in bringing products to market. This article aims to clarify these differences and provide insights into their systems, types, and effective management techniques.
Understanding the Distinction Between Manufacturing and Production
Manufacturing and production are foundational concepts in the business landscape. While both are essential for creating goods, they operate under different principles and methodologies. Manufacturing specifically refers to the process of converting raw materials into finished products. This process often involves complex machinery, labor, and technology to create items at scale. For instance, in the automotive industry, manufacturing includes the intricate assembly of various components such as engines, chassis, and electrical systems, all of which require precision engineering and quality control to ensure safety and reliability.
In contrast, production encompasses a broader range of activities, which includes not only manufacturing but also the methods of delivering services. In essence, production can represent everything from creating physical products to assembling components and even delivering intangible services to consumers. This can include the production of software, where developers create applications through coding and testing, or the production of content in media, where producers coordinate the efforts of writers, directors, and actors to create films and television shows. The diversity within production highlights its significance across various sectors, demonstrating how it adapts to meet the needs of different markets and consumer demands.
Moreover, the distinction between manufacturing and production is also evident in their respective supply chains. Manufacturing often relies on a just-in-time inventory system to minimize waste and reduce costs, requiring precise coordination with suppliers to ensure that materials arrive exactly when needed. On the other hand, production may involve a more flexible approach, allowing for adjustments based on consumer feedback or market trends. This adaptability is crucial in industries such as fashion and technology, where rapid changes in consumer preferences can dictate the pace and style of production. Understanding these nuances not only helps businesses optimize their operations but also allows them to innovate and respond effectively to an ever-evolving marketplace.
Overview of Manufacturing and Production Systems
Manufacturing systems are often categorized into different types based on how products are made. These include assembly lines, flexible manufacturing systems, and continuous manufacturing processes. Each system has distinct characteristics that impact efficiency, cost, and agility. For instance, assembly lines are designed for high-volume production of standardized products, allowing for streamlined operations and reduced labor costs. In contrast, flexible manufacturing systems offer the ability to adapt to changes in product design and volume, making them ideal for industries that require customization and quick turnaround times. Continuous manufacturing processes, often utilized in industries such as chemicals and food production, focus on the uninterrupted flow of materials, which maximizes output and minimizes waste.
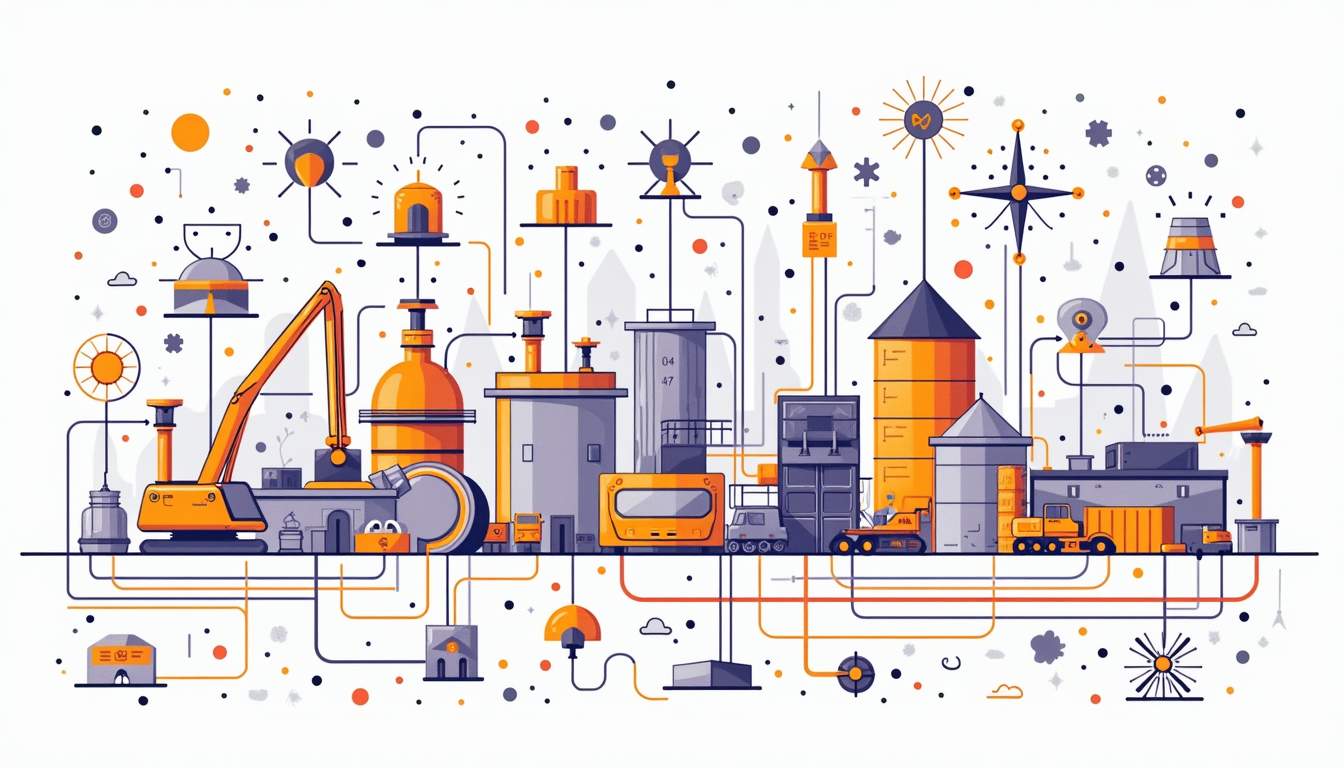
On the other hand, production systems are more versatile and can be classified based on their operational strategies. These may include continuous production, batch production, and project-based production, reflecting the various methods businesses employ to meet consumers' demands. Continuous production is characterized by the ongoing production of goods without interruption, which is particularly beneficial in industries where demand is steady and predictable. Batch production, however, involves producing goods in groups or batches, allowing for greater flexibility and the ability to switch between different products based on market needs. Project-based production is often seen in industries such as construction or software development, where unique, one-off projects require a tailored approach to resource allocation and scheduling. This diversity in production systems enables manufacturers to optimize their operations and respond effectively to changing market conditions and consumer preferences.
Exploring the Three Main Types of Manufacturing
When examining manufacturing, it becomes evident that there are primarily three types of manufacturing processes: job production, batch production, and mass production. Each method offers unique approaches to manufacturing that cater to different market demands.
Key Characteristics of Each Manufacturing Type
Job production refers to producing items individually or in small quantities, often customized to meet specific client needs. This approach offers flexibility but may require more time and resources. Industries such as bespoke furniture, custom jewelry, or specialized machinery often utilize job production, allowing artisans to focus on quality and detail. The downside, however, is that the costs are typically higher, and the production time can be significantly longer, which may not align with the fast-paced demands of some markets.
Conversely, batch production involves producing goods in groups or batches. This method allows for a balance of customization and efficiency, making it popular among makers of baked goods or apparel. In batch production, manufacturers can switch between different products, allowing for seasonal variations and limited runs that cater to changing consumer preferences. This flexibility can lead to reduced waste, as production can be adjusted based on demand forecasts. However, managing the transition between batches can introduce complexities in scheduling and inventory management.
Lastly, mass production is the most intensive type, where items are produced on a large scale using assembly lines. This method is highly efficient and enables lower costs per unit, making it suitable for consumer staples like automobiles and electronics. The hallmark of mass production is its reliance on standardized processes and machinery, which can lead to significant economies of scale. However, this efficiency comes at the cost of flexibility; once a production line is set up, it can be challenging to pivot to new designs or products without incurring substantial downtime and costs. Additionally, the focus on high volume can sometimes lead to a compromise in product quality, which manufacturers must carefully manage to maintain brand reputation.
The Three Primary Types of Production in Business
In the broader scope of production, there are three main types that define how businesses operate: job production, batch production, and mass production. Understanding these categories can help businesses tailor their operations for maximum efficiency.
Comparing Job Production, Batch Production, and Mass Production
As mentioned previously, job production excels at customization but at a higher cost and time commitment. On the other hand, batch production strikes a balance between efficiency and customizability, while mass production focuses on volume and cost-effectiveness.
Each type comes with its challenges and benefits, compelling organizations to choose an approach that aligns best with their business models and consumer expectations. For instance, job production is often favored by artisans and bespoke manufacturers who prioritize quality and uniqueness over quantity. In contrast, mass production is typically employed by large-scale manufacturers, such as automotive companies, where the goal is to produce large quantities of standardized products at the lowest possible cost. Understanding these nuances allows businesses to better position themselves in the market and meet specific consumer demands.
How to Create SKU Numbers Using Excel Templates
Creating SKU (Stock Keeping Unit) numbers is essential for inventory management. Using Excel templates can streamline this process significantly. To start, identify key attributes for your products, such as size, color, and type.
Once those elements are determined, you can set up an Excel template using columns for each attribute. Formulas can be utilized to automatically generate SKU numbers based on the selected characteristics, ensuring accuracy and consistency. Additionally, incorporating a system for tracking inventory levels alongside your SKU numbers can provide real-time insights into stock availability, helping to prevent overstocking or stockouts. This proactive approach not only enhances operational efficiency but also improves customer satisfaction by ensuring that popular items are always available for purchase.
Defining Average Order Value: Insights and Tips
Average Order Value (AOV) is a critical metric for assessing the efficiency of sales strategies. AOV calculates the average total of every order placed, which helps businesses optimize pricing and inventory strategies. Increasing this value can lead to higher revenues without significantly increasing customer acquisition costs.
Businesses can boost AOV by upselling products, offering discounts on minimum order quantities, or providing bundles that encourage customers to buy more. Tracking AOV regularly can reveal patterns and help refine marketing efforts. For instance, analyzing AOV in conjunction with customer demographics can uncover valuable insights, allowing businesses to tailor their promotions and product offerings to specific segments. Furthermore, seasonal trends can also impact AOV, making it crucial for businesses to adapt their strategies accordingly, ensuring they capitalize on peak shopping periods while maintaining customer engagement throughout the year.
Effective Inventory Management Techniques for Direct-to-Consumer Stores
In a digital-driven shopping landscape, efficient inventory management is paramount, especially for direct-to-consumer (DTC) brands. Managing stock levels effectively ensures that products are available without overwhelming the storage capacity. The rise of e-commerce has made it essential for DTC brands to adapt their inventory strategies to meet customer expectations for quick delivery and product availability. This shift not only enhances customer satisfaction but also builds brand loyalty, as consumers are more likely to return to a store that consistently meets their needs.
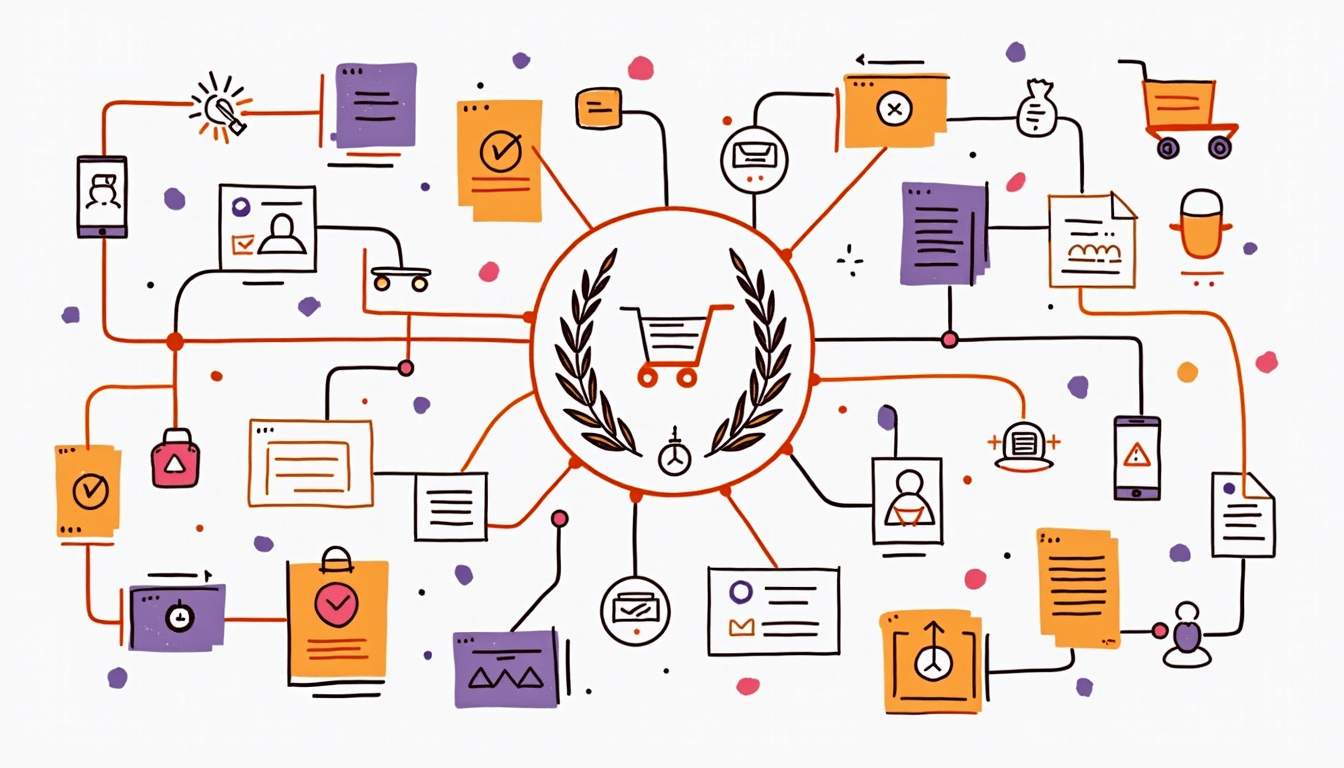
Utilizing just-in-time inventory, real-time tracking systems, and predictive analytics can provide better control over inventory levels, helping reduce waste and improve cash flow. By leveraging technology, businesses can forecast demand more accurately, allowing them to align their purchasing decisions with consumer behavior. This proactive approach minimizes the risk of overstocking or stockouts, both of which can significantly impact a brand's reputation and financial performance.
Strategies for Optimizing Inventory Levels
One way to optimize inventory levels is through categorization. By classifying items based on sales velocity, businesses can prioritize stock on fast-moving items while reducing restock frequency for slower-moving products. This method not only streamlines the inventory process but also helps in identifying which products may need promotional support to boost sales. By analyzing sales data, brands can determine if certain items are consistently underperforming and make strategic decisions about discontinuing or discounting them.
Additionally, implementing inventory management software can provide visibility into stock cycles, seasonality adjustments, and trends, ultimately leading to more informed decisions about restocking and managing supplies. Advanced software solutions often come equipped with features such as automated alerts for low stock levels and integration with e-commerce platforms, which can facilitate seamless order processing. Moreover, these systems can analyze historical sales data to identify patterns that inform future inventory purchases, ensuring that businesses are always prepared for seasonal spikes or shifts in consumer preferences.
What Does Optimum Stock Level Mean?
Optimum stock level refers to the ideal quantity of inventory that minimizes costs while ensuring it meets consumer demands. Striking this balance is vital for preventing overstocking or stockouts. An effective inventory management strategy hinges on understanding this concept, as it directly impacts a company's operational efficiency and financial health.
Businesses can assess their optimum stock levels by studying sales patterns, understanding lead times for supply orders, and evaluating market demand fluctuations. Additionally, incorporating advanced analytics and inventory management software can provide deeper insights into purchasing trends and customer preferences, allowing for more precise stock level adjustments.
The Importance of Maintaining Optimum Stock Levels
Maintaining optimum stock levels helps businesses reduce costs associated with holding excess inventory and ensures that products are available to meet customer needs. By doing so, companies can enhance customer satisfaction and foster loyalty, which is particularly important in today’s competitive landscape. A well-managed inventory system not only supports sales but also strengthens the brand's reputation, as customers are more likely to return to a business that consistently meets their needs.
Regularly reviewing stock levels and adjusting based on forecasting models enables businesses to stay relevant in an ever-changing market. This proactive approach allows companies to respond swiftly to unexpected demand surges or supply chain disruptions, ultimately safeguarding their market position. Furthermore, leveraging technology such as real-time inventory tracking can provide businesses with the agility needed to adapt to consumer trends, ensuring they remain one step ahead of competitors while optimizing their operational costs.
The Rationale Behind Batch Production in Manufacturing
Batch production serves as a bridge between job and mass production, offering flexibility and efficiency. This method allows manufacturers to produce goods in groups, enabling them to switch between product types without extensive downtime. By grouping similar items together, manufacturers can optimize their use of machinery and labor, reducing the overall production time and costs associated with setting up for different product lines.
This approach is particularly advantageous for companies looking to offer seasonal items or limited-time products while maintaining cost efficiency. For instance, a bakery may produce a batch of pumpkin spice muffins during the fall season, allowing them to capitalize on consumer demand while minimizing waste and maximizing output. The ability to adapt quickly to market trends can be a significant competitive advantage in today’s fast-paced economy.
Pros and Cons of Batch Production Methods
Batch production has its benefits, notably in versatility and reduced lead times. It allows businesses to respond to customer demands more effectively, as they can produce a variety of products in smaller quantities without the need for extensive retooling. This flexibility can lead to increased customer satisfaction and loyalty, as companies can offer a diverse range of products that cater to different tastes and preferences. However, it comes with its drawbacks, such as increased complexity in planning and potential disruptions in workflows if changes are made frequently. The need for precise scheduling and inventory management can strain resources, especially for smaller manufacturers.
Ultimately, the effectiveness of batch production varies from one business model to another, and careful consideration should guide the decision to adopt this method. Companies must assess their production capabilities, market demands, and financial implications to determine if batch production aligns with their strategic goals. Additionally, investing in technology and training can enhance the efficiency of batch production processes, helping businesses to mitigate some of the challenges associated with this method. As industries evolve, the integration of automation and data analytics into batch production could further streamline operations, paving the way for innovative manufacturing solutions.
Understanding Make to Stock Strategy: Benefits and Drawbacks
The Make to Stock (MTS) production strategy emphasizes building inventory based on anticipated customer demand. This approach can lead to high efficiency, as it allows organizations to produce goods in bulk to meet predictable market needs. However, it also carries risks related to overproduction, where unsold products may lead to increased holding costs. In industries with stable demand patterns, such as consumer goods or electronics, MTS can streamline operations and reduce lead times, ensuring that products are readily available when customers are ready to purchase.
Consequently, businesses must balance their forecasting accuracy with production capabilities to optimize their make to stock strategies. This balance is crucial, as inaccurate forecasts can result in either excess inventory or stockouts, both of which can negatively impact customer satisfaction and overall profitability. Companies often employ various forecasting techniques, including historical sales data analysis and market trend evaluations, to improve their predictions. Additionally, leveraging advanced technologies such as artificial intelligence and machine learning can enhance forecasting precision, allowing organizations to respond more agilely to market fluctuations.
Moreover, the MTS strategy can significantly affect supply chain dynamics. By maintaining a buffer stock, companies can mitigate the risks associated with supply chain disruptions, such as delays from suppliers or sudden spikes in demand. However, this approach necessitates careful management of relationships with suppliers and logistics partners to ensure that inventory levels are maintained without incurring excessive costs. Furthermore, the environmental implications of MTS cannot be overlooked; organizations are increasingly pressured to adopt sustainable practices, which may require reevaluating inventory levels and production methods to minimize waste and reduce their carbon footprint.
Inventory Control Explained: Definitions and Techniques
Inventory control is the process of managing stock levels to ensure that the right amount of products are available at the right time. This includes tracking inventory turnover, order levels, and stock quantities to minimize losses and maximize sales. Effective inventory control is crucial for businesses of all sizes, as it directly impacts cash flow, customer satisfaction, and overall operational efficiency. By maintaining a keen eye on inventory metrics, companies can avoid the pitfalls of overstocking or stockouts, which can lead to lost sales and dissatisfied customers.
Effective inventory control techniques include the use of ABC analysis, where items are categorized into three groups based on their significance, as well as cycle counting, which involves regular checks to maintain accuracy in stock records. This categorization helps businesses focus their efforts on the most critical items, ensuring that high-value products are always in stock while allowing for more lenient management of lower-value items. Additionally, employing techniques like Just-In-Time (JIT) inventory can further enhance efficiency by reducing holding costs and ensuring that products arrive only as they are needed in the production process.
Methods for Effective Inventory Management
Implementing technology, such as an integrated inventory management system, can significantly enhance efficiency. This allows for better data analysis and provides insights into sales trends that inform future stocking decisions. Modern inventory management solutions often come equipped with features such as real-time tracking, automated reordering, and detailed reporting capabilities, which can help businesses make informed decisions quickly. Furthermore, cloud-based systems enable access to inventory data from anywhere, facilitating better collaboration among teams and improved responsiveness to market changes.
Additionally, establishing re-order points and labeling systems for quick identification of stock items can streamline the inventory management process. By combining technology with proven techniques, businesses can ensure they maintain optimal inventory levels, meet customer expectations, and ultimately succeed in their markets. Training staff on best practices for inventory handling and management is equally important; well-informed employees can make significant contributions to maintaining accuracy and efficiency. Regular audits and performance reviews of inventory processes can also help identify areas for improvement, ensuring that the inventory management strategy evolves in tandem with the business's growth and changing market dynamics.