Common Mistakes When Managing a Bill of Materials in E-Commerce and How to Avoid Them
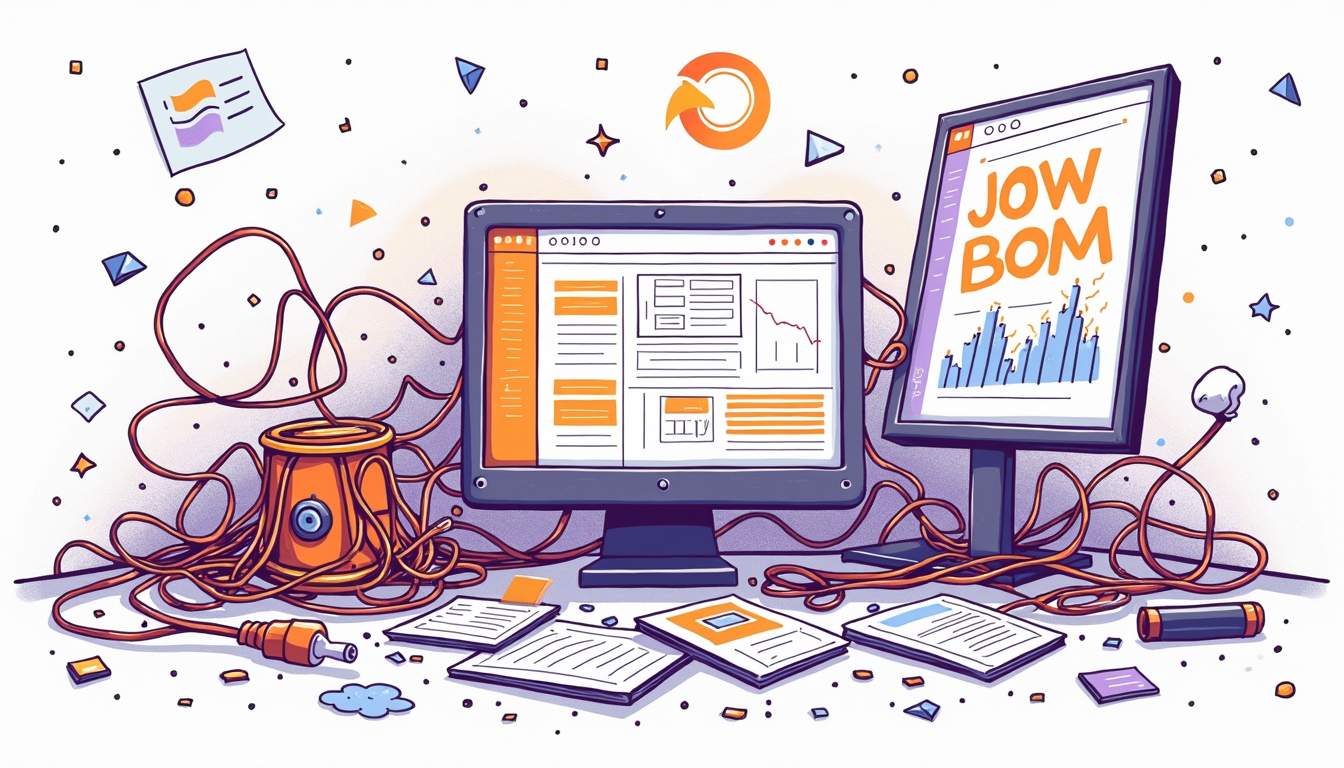
In the fast-paced world of e-commerce, managing a Bill of Materials (BOM) effectively is crucial for ensuring smooth operations and maintaining profitability. A BOM is essentially a comprehensive list of raw materials, components, and instructions required to manufacture, assemble, or repair a product. While it may seem straightforward, there are several common pitfalls that businesses encounter when handling BOMs. Understanding these mistakes and knowing how to avoid them can save time, reduce costs, and improve overall efficiency.
Understanding the Importance of a Bill of Materials
A Bill of Materials serves as the backbone of product manufacturing and inventory management. It provides a detailed breakdown of every item needed to produce a product, ensuring that nothing is overlooked. In e-commerce, where product offerings can be vast and varied, a well-managed BOM helps streamline production processes and inventory control.
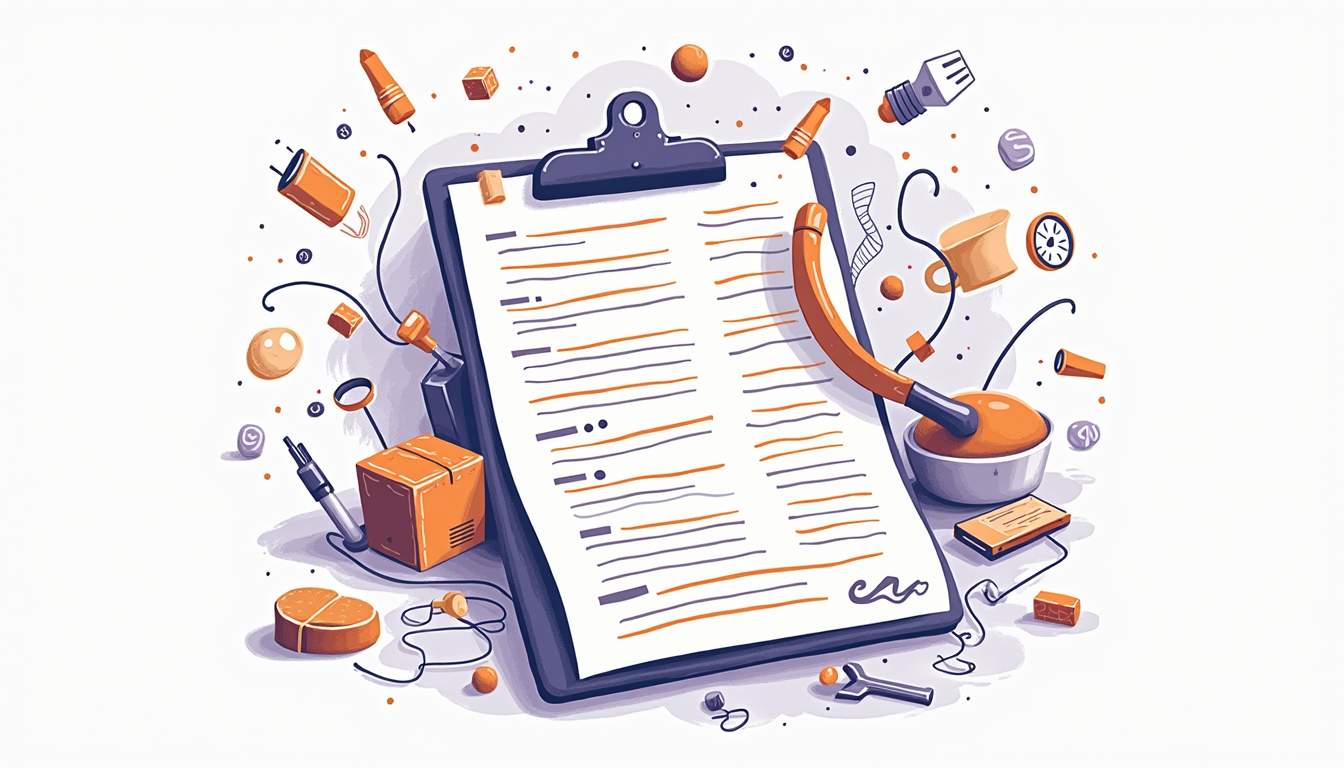
Without a precise BOM, businesses risk overstocking or understocking components, leading to increased costs or production delays. Furthermore, inaccuracies in a BOM can result in product defects, customer dissatisfaction, and potential damage to the brand's reputation. Thus, understanding the critical role of a BOM is the first step towards effective management.
Moreover, a BOM is not just a static document; it is a dynamic tool that evolves with product changes, updates, and improvements. Keeping it accurate and up-to-date is essential for maintaining the integrity of the production process and ensuring that the final product meets quality standards.
Common Mistakes in BOM Management
1. Incomplete or Inaccurate Data
One of the most frequent mistakes in managing a BOM is having incomplete or inaccurate data. Missing information or errors in the list of components can lead to production delays and increased costs. For instance, if a critical component is not listed, it may not be ordered in time, halting production.
To avoid this, it is essential to regularly review and update the BOM. Implementing a system for cross-verifying data entries can help catch errors early. Additionally, involving multiple team members in the review process can provide a fresh perspective and catch mistakes that might have been overlooked.
2. Lack of Version Control
In e-commerce, products often undergo changes and improvements, which necessitates updates to the BOM. Without proper version control, it can be challenging to track these changes, leading to confusion and errors in production.
Implementing a robust version control system ensures that all stakeholders are aware of the latest BOM version. This can be achieved through software solutions that automatically track changes and notify relevant team members. Clear labeling of BOM versions and maintaining a change log can further enhance version control.
3. Ignoring Supplier Lead Times
Another common mistake is failing to consider supplier lead times when managing a BOM. Each component may have different lead times, and not accounting for these can result in production delays.
To mitigate this, businesses should establish strong communication channels with suppliers to ensure accurate lead time information. Incorporating buffer times into the production schedule can also help accommodate any unexpected delays, ensuring that production remains on track.
Strategies to Avoid BOM Management Mistakes
1. Implementing Automation Tools
Automation tools can significantly enhance BOM management by reducing manual errors and streamlining processes. These tools can automatically update BOMs, track changes, and generate reports, freeing up valuable time for team members to focus on strategic tasks.
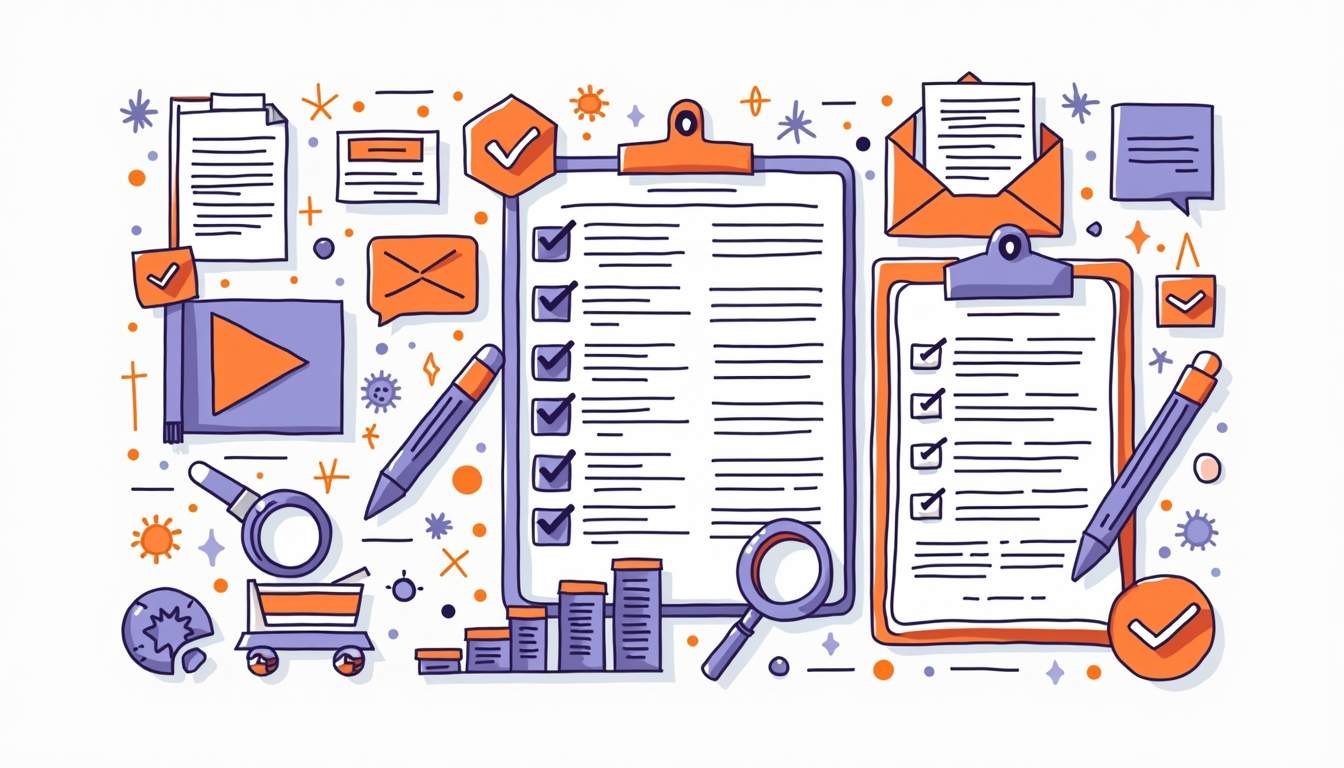
When selecting an automation tool, consider features such as integration capabilities with existing systems, user-friendliness, and scalability. A tool that can grow with your business will provide long-term benefits and support efficient BOM management.
2. Regular Training and Development
Ensuring that team members are well-trained in BOM management is crucial for avoiding common mistakes. Regular training sessions can keep staff updated on best practices, new tools, and industry trends.
Encouraging a culture of continuous learning and development can also foster innovation and improvement in BOM management processes. Providing access to resources such as webinars, workshops, and industry conferences can further enhance team knowledge and skills.
3. Establishing Clear Communication Channels
Effective communication is key to successful BOM management. Establishing clear communication channels between departments, suppliers, and stakeholders can prevent misunderstandings and ensure that everyone is on the same page.
Regular meetings and updates can facilitate information sharing and collaboration. Utilizing communication tools such as project management software can also enhance transparency and accountability, ensuring that BOM management processes run smoothly.
The Role of Technology in BOM Management
Technology plays a pivotal role in modern BOM management. Advanced software solutions offer features such as real-time updates, data analytics, and integration with other business systems, providing a comprehensive view of the production process.
Investing in technology can provide a competitive edge by improving accuracy, efficiency, and scalability. As the e-commerce landscape continues to evolve, staying ahead with the latest technological advancements can help businesses adapt and thrive.
Moreover, technology can facilitate collaboration and communication across teams and locations, breaking down silos and fostering a more cohesive approach to BOM management. By leveraging technology, businesses can enhance their ability to respond to market changes and customer demands swiftly and effectively.
Conclusion
Managing a Bill of Materials in e-commerce requires careful attention to detail and a proactive approach to avoid common pitfalls. By understanding the importance of a BOM, recognizing common mistakes, and implementing effective strategies, businesses can optimize their production processes and maintain a competitive edge.
Embracing technology, fostering a culture of continuous learning, and establishing clear communication channels are key to successful BOM management. As the e-commerce industry continues to grow and evolve, businesses that prioritize efficient BOM management will be well-positioned to meet the challenges and opportunities of the future.