Cost-Benefit Analysis of Inventory: A Comprehensive Guide
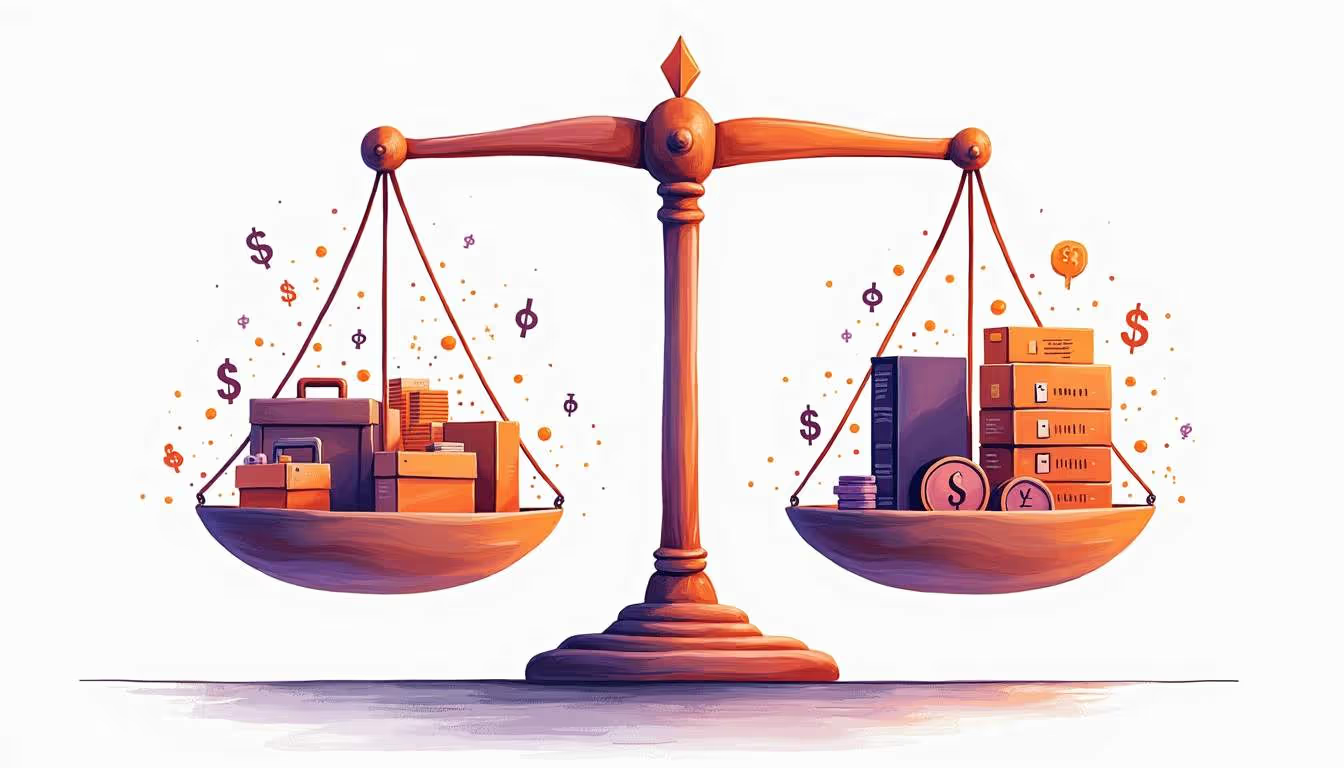
In the world of business, inventory management plays a crucial role in determining the success and efficiency of operations. Conducting a cost-benefit analysis of inventory can help businesses make informed decisions about how much inventory to hold, when to reorder, and how to optimize their supply chain. This analysis involves weighing the costs associated with holding and managing inventory against the benefits it provides. Understanding this balance is key to improving profitability and ensuring smooth business operations.
Understanding the Basics of Inventory Cost-Benefit Analysis
What is Inventory Cost-Benefit Analysis?
Inventory cost-benefit analysis is a systematic approach to evaluating the financial implications of inventory management decisions. It involves assessing the costs associated with holding inventory, such as storage, insurance, and obsolescence, against the benefits, such as meeting customer demand, reducing lead times, and taking advantage of bulk purchasing discounts. This analysis helps businesses determine the optimal level of inventory that maximizes profitability while minimizing costs.
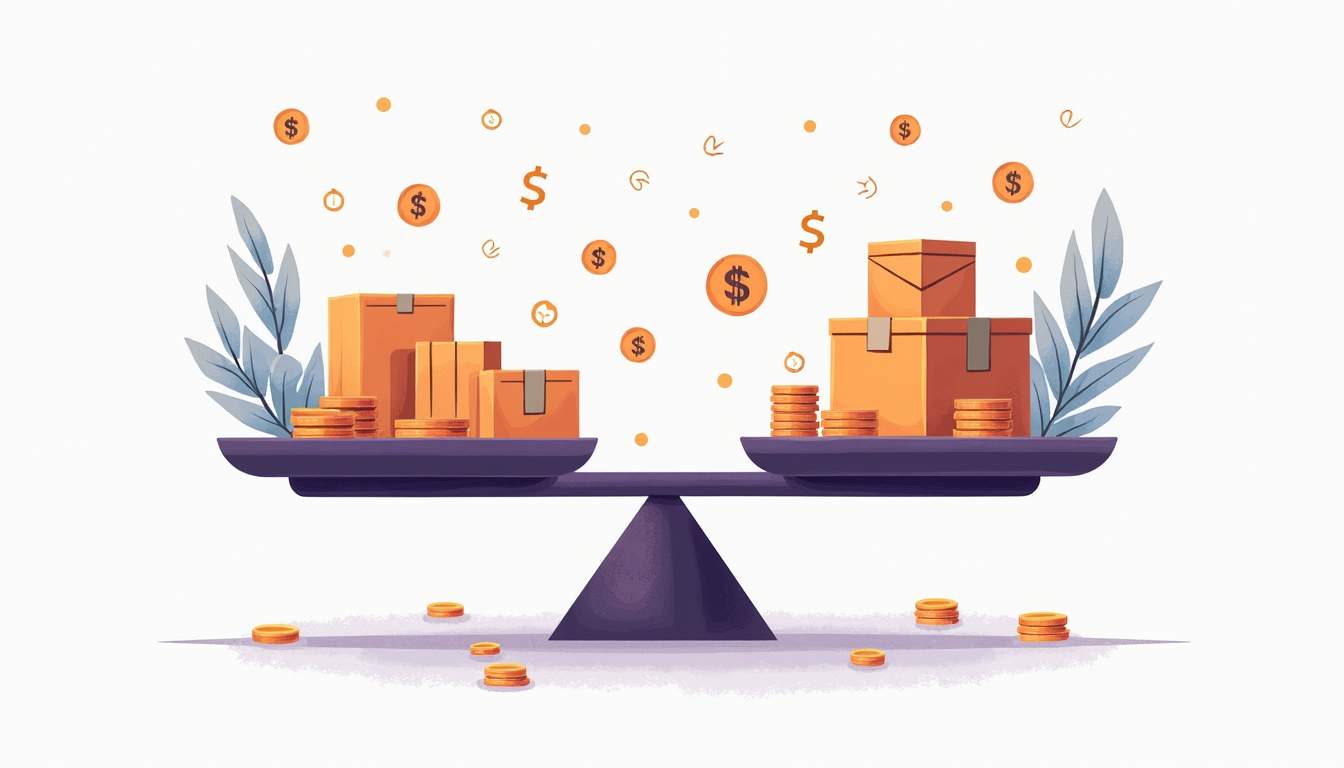
The Importance of Inventory Management
Effective inventory management is essential for businesses to maintain a competitive edge. It ensures that products are available when customers need them, which enhances customer satisfaction and loyalty. Additionally, proper inventory management helps reduce waste, lower storage costs, and improve cash flow. By conducting a cost-benefit analysis, businesses can identify areas where they can optimize their inventory levels and improve overall efficiency.
Key Components of Inventory Costs
Inventory costs can be categorized into several components, each of which plays a significant role in the cost-benefit analysis. These components include:
- Holding Costs: These are the costs associated with storing unsold goods, including warehousing, insurance, and depreciation.
- Ordering Costs: These costs are incurred every time an order is placed, including administrative expenses and transportation costs.
- Shortage Costs: Costs that arise when inventory levels are insufficient to meet demand, leading to lost sales and customer dissatisfaction.
- Obsolescence Costs: The costs associated with inventory that becomes outdated or unsellable.
Benefits of Maintaining Optimal Inventory Levels
Meeting Customer Demand
One of the primary benefits of maintaining optimal inventory levels is the ability to meet customer demand promptly. Having the right amount of stock on hand ensures that businesses can fulfill orders quickly, leading to increased customer satisfaction and repeat business. This is particularly important in industries where customer expectations for fast delivery are high.
Reducing Lead Times
By keeping adequate inventory levels, businesses can reduce lead times, which is the time taken from receiving an order to delivering the product to the customer. Shorter lead times enhance the customer experience and can provide a competitive advantage. Additionally, reduced lead times can help businesses respond more quickly to market changes and customer preferences.
Taking Advantage of Economies of Scale
Maintaining optimal inventory levels allows businesses to take advantage of economies of scale. By purchasing in bulk, companies can negotiate better prices with suppliers, reducing the cost per unit. This not only lowers overall inventory costs but also improves profit margins. A cost-benefit analysis can help determine the ideal order quantity that maximizes these savings.
Steps to Conduct a Cost-Benefit Analysis of Inventory
Identify and Quantify Costs
The first step in conducting a cost-benefit analysis is to identify and quantify all relevant inventory costs. This includes calculating holding costs, ordering costs, shortage costs, and obsolescence costs. Accurate cost estimation is crucial for making informed decisions. Businesses should also consider indirect costs, such as the impact of inventory levels on cash flow and working capital.
Estimate the Benefits
Next, businesses should estimate the benefits associated with maintaining optimal inventory levels. This includes quantifying the potential increase in sales due to improved customer satisfaction, the cost savings from reduced lead times, and the financial advantages of bulk purchasing. Estimating these benefits requires a thorough understanding of the business's operations and market dynamics.
Analyze the Data
Once the costs and benefits have been quantified, the next step is to analyze the data to determine the optimal inventory level. This involves comparing the total costs with the total benefits to identify the inventory level that maximizes net benefits. Businesses can use various analytical tools and models, such as the Economic Order Quantity (EOQ) model, to assist in this analysis.
Implement and Monitor
After determining the optimal inventory level, businesses should implement the findings and continuously monitor inventory performance. Regularly reviewing inventory levels and adjusting them based on changing market conditions and business needs is essential for maintaining efficiency. Monitoring also helps identify any discrepancies between expected and actual outcomes, allowing for timely corrective actions.
Challenges in Conducting Inventory Cost-Benefit Analysis
Data Accuracy and Availability
One of the significant challenges in conducting a cost-benefit analysis is ensuring data accuracy and availability. Inaccurate data can lead to incorrect conclusions and suboptimal inventory decisions. Businesses need reliable data sources and effective data management systems to ensure the accuracy of their analysis.
Dynamic Market Conditions
Market conditions are constantly changing, and businesses must adapt their inventory strategies accordingly. Factors such as seasonal demand fluctuations, economic shifts, and changes in consumer preferences can impact inventory requirements. Conducting regular cost-benefit analyses helps businesses stay agile and responsive to these changes.
Complexity of Inventory Systems
Inventory systems can be complex, especially for businesses with diverse product lines and multiple locations. Managing this complexity requires sophisticated inventory management software and skilled personnel. Businesses must invest in the right tools and training to effectively conduct cost-benefit analyses and optimize their inventory systems.
Conclusion
Conducting a cost-benefit analysis of inventory is a vital process for businesses aiming to optimize their inventory management strategies. By carefully evaluating the costs and benefits associated with different inventory levels, businesses can make informed decisions that enhance profitability, improve customer satisfaction, and maintain a competitive edge. Despite the challenges involved, the insights gained from a thorough analysis can lead to significant improvements in operational efficiency and financial performance.
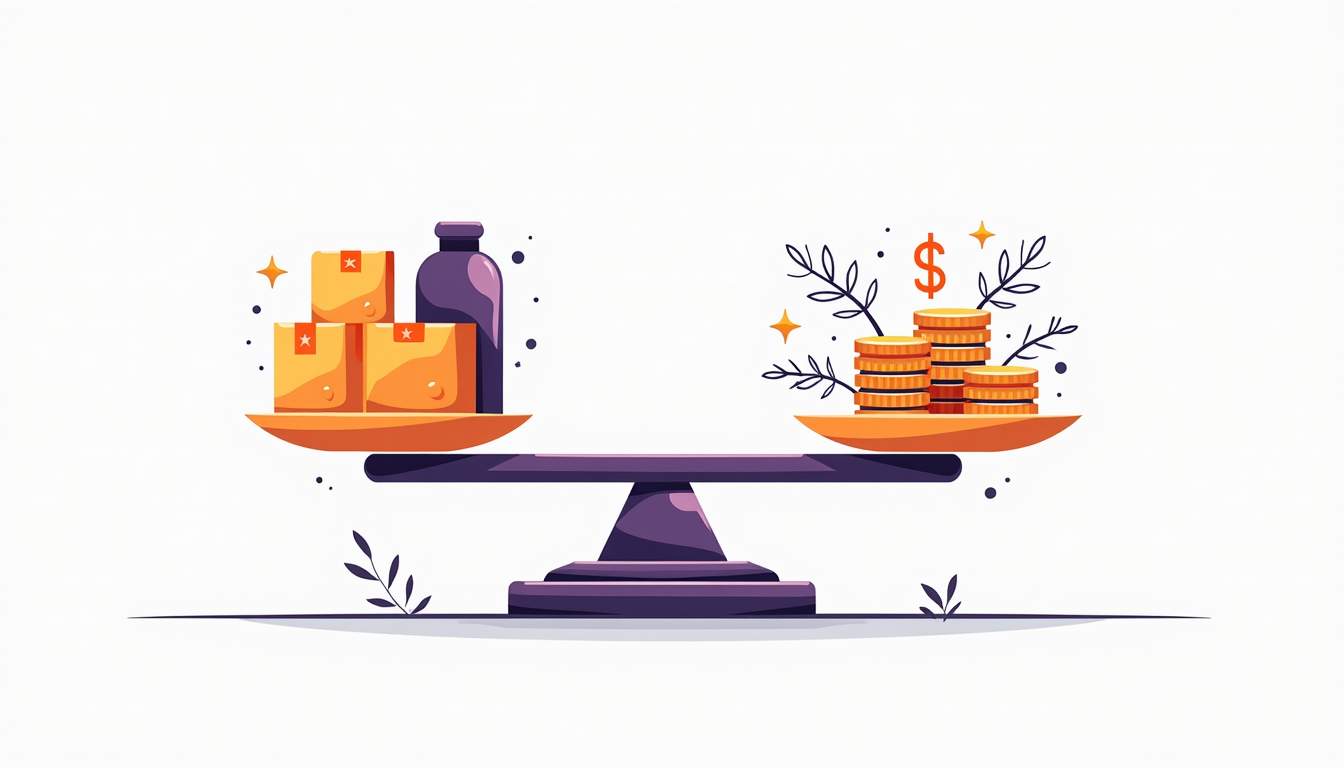