Essential Guide to Conducting an Effective Inventory Audit
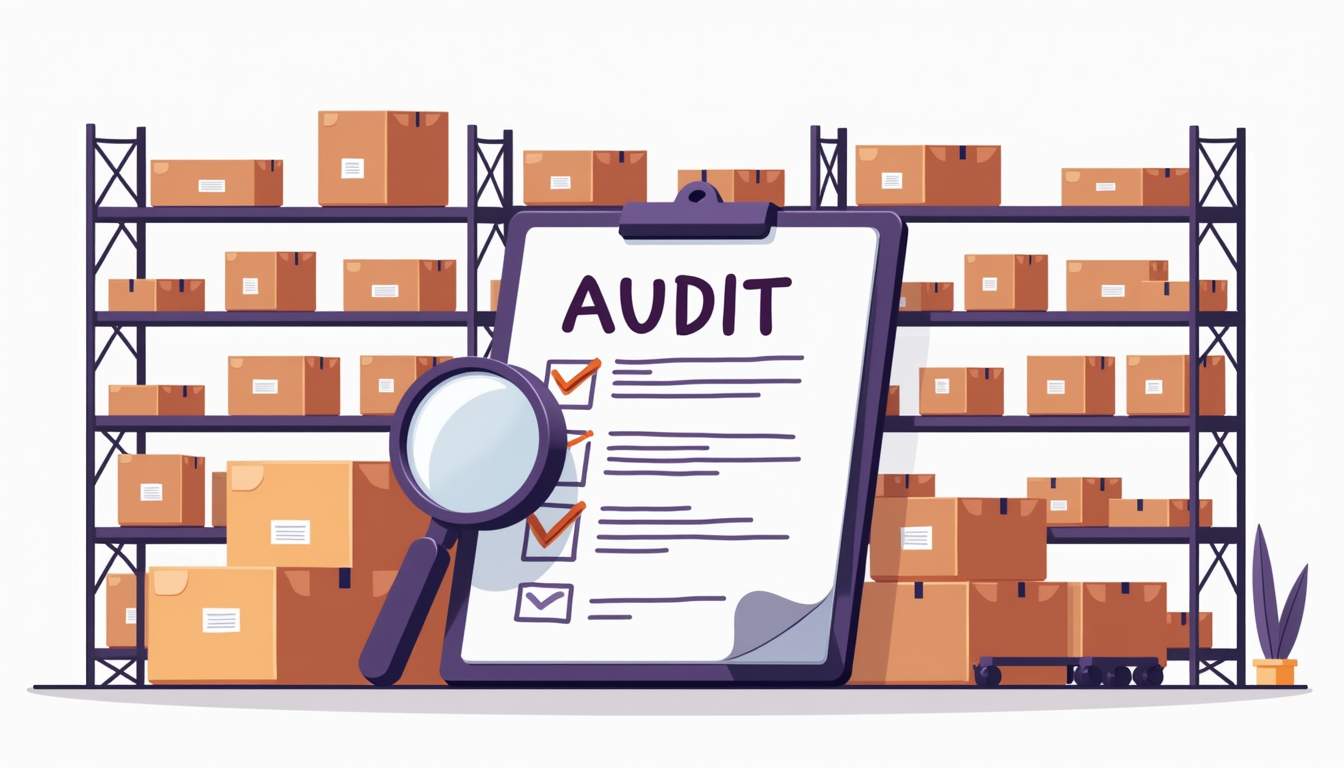
Inventory audits are a crucial process for businesses of all sizes. They not only help in maintaining the accuracy of your inventory records but also ensure financial integrity and operational efficiency. This guide aims to provide you with a comprehensive overview of conducting an effective inventory audit by examining various key aspects, practical use cases, and essential steps involved. Let’s dive in!
Overview
An inventory audit is a systematic examination of your inventory records and physical stock. This process helps organizations identify discrepancies, evaluate operational efficiencies, and ensure compliance with regulatory standards. The audit can be conducted as a full count or a sample count, depending on the needs of the organization. A full count involves a thorough verification of every item in stock, which can be time-consuming but provides a comprehensive view of inventory accuracy. On the other hand, a sample count focuses on a representative subset of inventory, which can save time and resources while still offering valuable insights into overall inventory health.
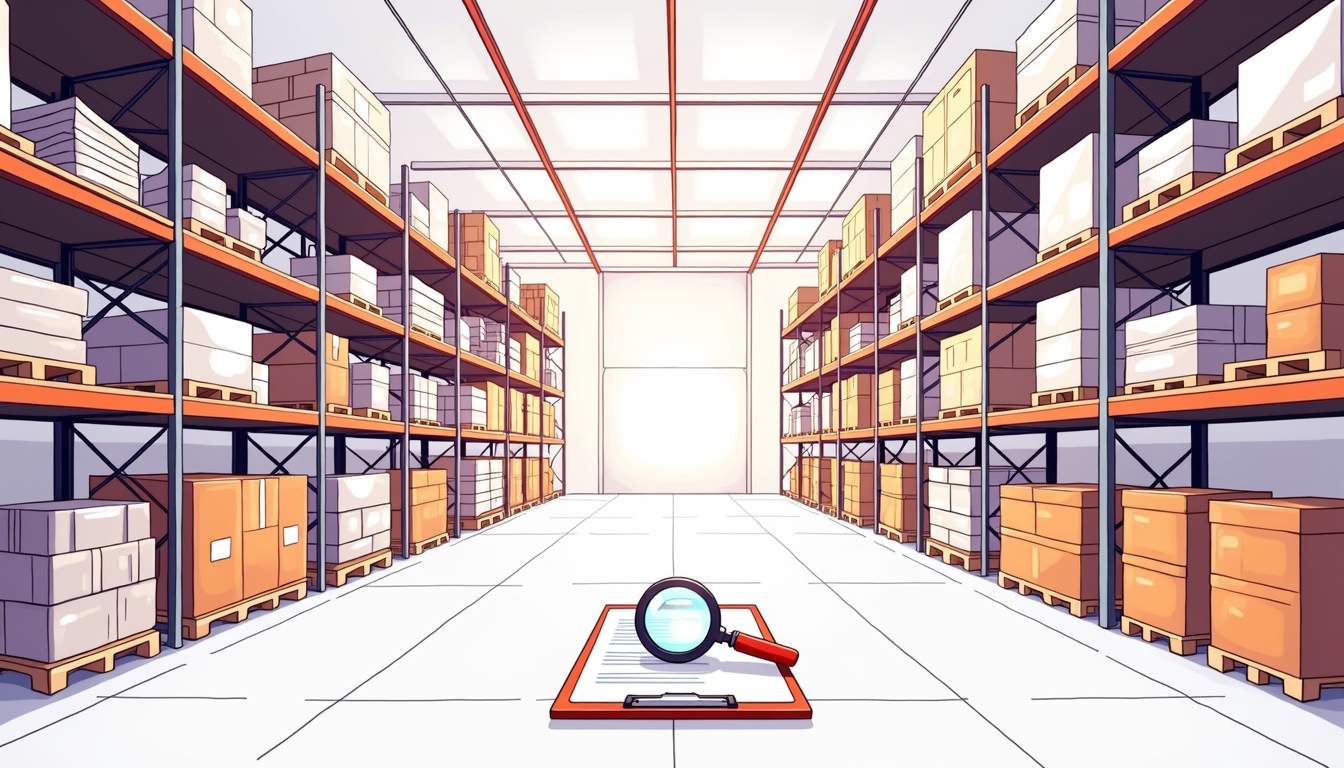
The frequency of inventory audits can vary—some businesses may choose to complete them annually, while others may conduct them quarterly or even monthly. Regardless of the chosen frequency, it is imperative to understand the audit process to maximize its effectiveness. Regular audits not only help in maintaining accurate records but also play a crucial role in identifying trends over time. For instance, frequent audits can reveal patterns in stock discrepancies, such as recurring issues with specific items or suppliers, allowing businesses to take proactive measures to address these challenges.
Additionally, the implementation of technology in inventory audits has transformed the way organizations approach this critical task. Many companies now utilize advanced inventory management software and barcode scanning systems to streamline the auditing process. These tools can significantly reduce human error, enhance data accuracy, and provide real-time insights into stock levels. Furthermore, integrating these technologies can facilitate better decision-making, as managers can quickly access detailed reports and analytics that inform purchasing strategies and inventory turnover rates.
Moreover, the importance of employee training cannot be overstated when it comes to conducting effective inventory audits. Ensuring that staff members are well-versed in audit procedures, inventory management systems, and compliance requirements is essential for a successful audit outcome. Regular training sessions can empower employees to take ownership of their roles in the inventory process, fostering a culture of accountability and precision that ultimately benefits the organization as a whole.
Key Features
There are several key features that make inventory audits effective. These features include accuracy, thoroughness, and transparency. Accuracy ensures that the data collected reflects the actual quantities available, while thoroughness examines each aspect of inventory management and control.
- Real-time Data Integration: Utilizing technology to provide up-to-date information enhances the audit process.
- Detailed Documentation: Keeping records of all findings enables more straightforward follow-ups and adjustments.
- Regulatory Compliance: Ensuring that your audits meet legal and financial requirements is critical.
When these features are implemented correctly, they improve the reliability and validity of the audit outcomes, making your inventory management practices more robust. Additionally, regular audits can help identify discrepancies early, allowing businesses to address issues before they escalate into larger problems. This proactive approach not only saves time and resources but also fosters a culture of accountability within the organization.
Moreover, effective inventory audits can lead to improved customer satisfaction. By ensuring that stock levels are accurate and reflective of actual availability, businesses can fulfill orders more efficiently and reduce instances of backorders or stockouts. This not only enhances the customer experience but also strengthens brand loyalty, as clients come to trust that their needs will be met promptly and reliably. As such, investing time and resources into a comprehensive audit process is not just a matter of compliance, but a strategic move that can yield significant long-term benefits.
Integration Options
Integrating inventory audit processes with existing systems is essential for streamlining operations. Many businesses utilize Enterprise Resource Planning (ERP) systems to manage inventory, sales, and financial data seamlessly. Here are some integration options:
- Warehouse Management Systems (WMS): These systems help track inventory levels, manage stock movement, and streamline the audit process.
- Point of Sale (POS) Systems: Integrating POS systems can provide valuable insights into inventory turnover rates, which is vital for audits.
- Accounting Software: Ensures that inventory data aligns with financial reports for a clearer understanding of asset values.
By leveraging integrations, businesses can ensure consistency and accuracy throughout the inventory audit process, reducing errors and increasing efficiency. Moreover, integrating these systems can facilitate real-time data sharing, allowing for immediate updates on stock levels and sales trends. This capability not only enhances decision-making but also empowers businesses to respond swiftly to market demands, minimizing the risk of overstocking or stockouts.
Additionally, advanced integration options such as cloud-based solutions offer scalability and flexibility, enabling businesses to adapt their inventory management processes as they grow. With the ability to access data from anywhere, teams can collaborate more effectively, ensuring that audit processes are not only accurate but also timely. As technology continues to evolve, exploring new integration possibilities will be crucial for maintaining a competitive edge in the market.
Practical Use Cases
Implementing inventory audits can provide significant benefits across various scenarios. Here are some practical use cases:
- Retail Businesses: Regular audits help optimize stock levels and reduce shrinkage, ensuring profitability.
- Manufacturing Sector: Audits assure that raw materials and finished goods are accounted for accurately, minimizing production downtime.
- Distribution Companies: These businesses often face logistical challenges, making regular audits essential for tracking inventory in real-time.
Each of these scenarios demonstrates the importance of keeping inventory reliable and ensuring operations run smoothly.
In addition to the aforementioned sectors, the healthcare industry also benefits significantly from routine inventory audits. Hospitals and clinics must maintain precise records of medical supplies, pharmaceuticals, and equipment to ensure patient safety and compliance with regulatory standards. By conducting regular audits, healthcare providers can identify discrepancies, reduce waste, and ensure that critical supplies are always available when needed. This not only enhances operational efficiency but also improves patient care outcomes, as timely access to necessary medical resources is crucial in emergency situations.
Moreover, the e-commerce sector has seen a transformative impact from inventory audits. With the rapid growth of online shopping, businesses must keep track of vast inventories across multiple platforms and warehouses. Regular audits in this space help to streamline order fulfillment processes, reduce shipping errors, and enhance customer satisfaction. By ensuring that inventory records are accurate, e-commerce companies can avoid overselling items, which can lead to negative customer experiences and damage to their brand reputation. Thus, the role of inventory audits extends beyond mere numbers; it is integral to maintaining trust and efficiency in a highly competitive market.
Relevant Industries
Inventory audits are applicable across numerous industries. Some relevant industries include:
- Food and Beverage: Strict regulations require accurate monitoring of inventory.
- Healthcare: Hospitals and clinics must maintain precise inventory for medical supplies and equipment.
- Retail: The fast-paced nature of retail necessitates regular audits to keep track of seasonal stock.
Understanding the diverse applications of inventory audits allows industries to tailor their auditing processes appropriately. In the food and beverage sector, for instance, not only do businesses have to comply with health regulations, but they also need to manage perishable goods effectively. This often involves implementing sophisticated inventory management systems that can track expiration dates and ensure that stock rotation practices are followed meticulously. Failure to do so can result in significant financial losses and damage to a brand's reputation.
Similarly, in the healthcare industry, the stakes are incredibly high when it comes to inventory management. Hospitals must ensure that they have the right quantities of essential supplies, such as medications and surgical instruments, readily available at all times. This requires a robust auditing process that can adapt to fluctuating demands, especially during crises like pandemics. Advanced technologies, such as RFID tracking and cloud-based inventory management systems, are increasingly being adopted to enhance accuracy and efficiency in tracking these critical resources.
Understanding Inventory Audits
To effectively conduct inventory audits, one must understand the components involved. At its core, the audit involves physically counting items and comparing them to recorded quantities in the inventory management system. Various methodologies – including full counts and cycle counts – can be utilized based on the scope and needs of the audit. Full counts are typically performed at the end of a financial period, providing a comprehensive snapshot of inventory levels, while cycle counts are ongoing and focus on specific items at regular intervals, allowing for a more manageable approach to inventory management.
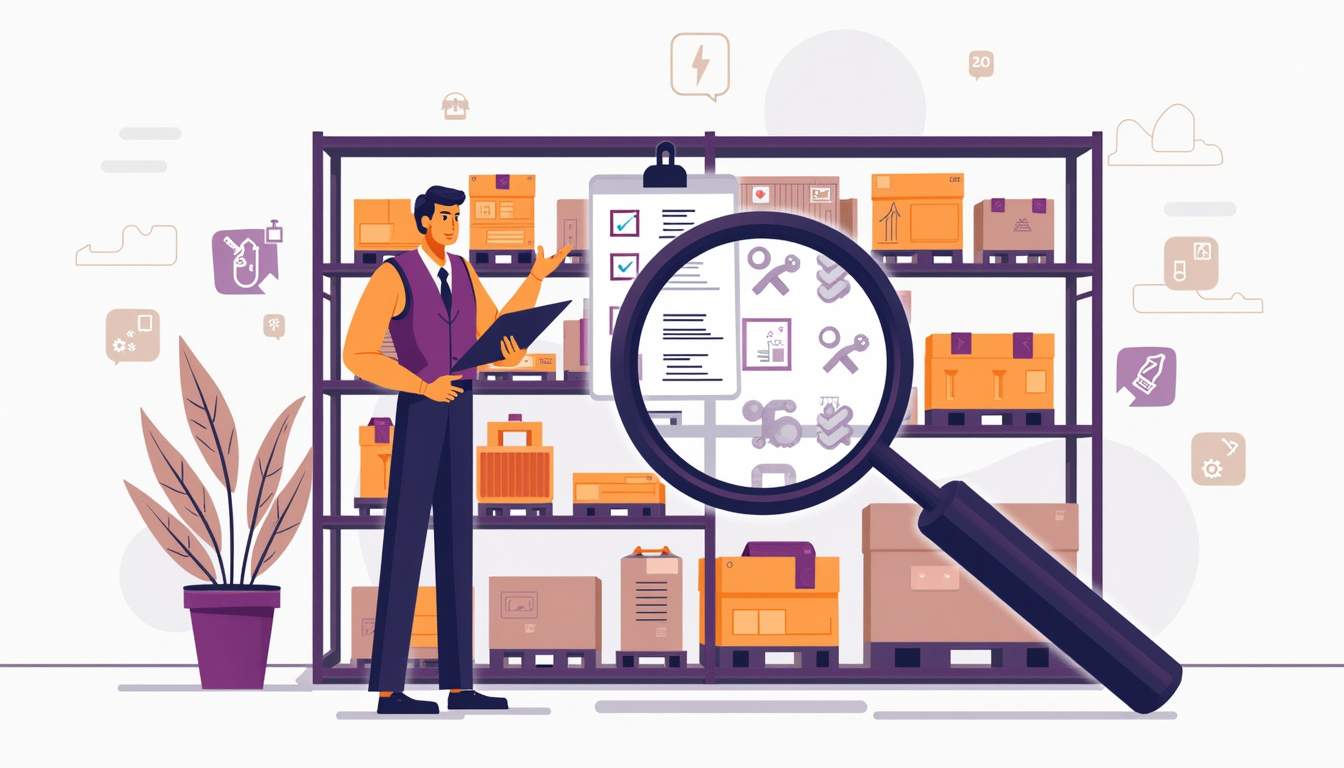
Furthermore, specific metrics should be analyzed during audits, such as accuracy ratios and turnover rates, which can provide insights into operational efficiency. Accuracy ratios indicate how closely the physical count matches the recorded count, while turnover rates measure how quickly inventory is sold and replaced over a period. By understanding these elements, businesses can better prepare for and conduct audits that yield useful information. Additionally, it's essential to consider the role of technology in modern inventory audits. Utilizing barcode scanners and RFID technology can streamline the counting process, reduce human error, and enhance data accuracy, making audits not only more efficient but also more reliable.
Moreover, the importance of employee training cannot be overstated. Ensuring that staff members are well-versed in the audit procedures and the use of technology can significantly impact the success of the audit process. Regular training sessions can help in reinforcing best practices and keeping the team updated on any changes in inventory management systems. Furthermore, fostering a culture of accountability and accuracy within the organization can lead to more diligent inventory practices, ultimately resulting in fewer discrepancies and a more robust inventory management system.
The Importance of Inventory Auditing
Inventory auditing plays a vital role in maintaining the overall health of any business. Regular audits help identify issues such as lost items, overstocking, and stockouts, which can lead to customer dissatisfaction and financial loss.
Moreover, inventory audits can enhance decision-making by providing data-backed insights into purchasing trends and inventory performance. This information empowers management to make strategic choices regarding stock replenishment, sales projections, and budgeting.
In addition to these benefits, inventory auditing also fosters accountability within the organization. When employees understand that regular audits will take place, they are more likely to handle inventory with care and diligence. This heightened sense of responsibility can lead to reduced shrinkage, which is a common issue in many retail environments. Furthermore, a culture of transparency and accuracy surrounding inventory management can improve overall operational efficiency, as teams work together to ensure that records are up-to-date and reflect the true state of stock.
Another significant aspect of inventory auditing is its impact on compliance and risk management. Many industries are subject to strict regulations regarding inventory management, particularly in sectors such as pharmaceuticals and food services. Regular audits help ensure that businesses adhere to these regulations, minimizing the risk of costly fines and legal issues. By maintaining accurate inventory records, companies can also better prepare for unexpected events, such as supply chain disruptions or sudden changes in market demand, allowing them to respond swiftly and effectively to maintain customer satisfaction.
Advantages of Conducting Inventory Audits
The advantages of conducting inventory audits extend beyond simply keeping track of stock levels. Here are some notable benefits:
- Enhanced Accuracy: Regular audits improve record accuracy, reducing the chances of errors.
- Cost Control: Identifying discrepancies can help minimize losses due to theft, damage, or obsolescence.
- Improved Cash Flow: Knowing the inventory turnover rates assists businesses in managing cash flow more effectively.
Overall, the benefits of conducting regular and thorough inventory audits have long-term implications for sustainability and growth. Additionally, inventory audits can lead to better decision-making processes. By having accurate data regarding stock levels and turnover rates, businesses can make informed choices about purchasing, production, and sales strategies. This data-driven approach not only enhances operational efficiency but also allows companies to respond more swiftly to market demands, thereby gaining a competitive edge.
Moreover, inventory audits foster a culture of accountability within an organization. When employees understand that regular audits will be conducted, they are more likely to take ownership of their roles in inventory management. This heightened sense of responsibility can lead to improved practices in handling goods, ultimately resulting in better service delivery to customers and a stronger reputation in the marketplace.
Steps Involved in Inventory Auditing
Conducting an inventory audit requires careful planning and execution. Here are the essential steps involved in the auditing process:
Conducting ABC Analysis
ABC analysis categorizes inventory items into three groups based on importance and value. Items classified as ‘A’ are critical and require tight control, while ‘C’ items are less significant. This categorization helps prioritize where to focus auditing efforts. By concentrating on high-value items, businesses can allocate resources more effectively, ensuring that the most impactful products are monitored closely. This strategic approach not only enhances inventory accuracy but also aids in identifying trends that may affect stock levels and sales performance.
Implementing Cut-off Analysis
Cut-off analysis involves ensuring that inventory records reflect accurate data by setting specific cut-off dates for counting and recording stock. This practice is particularly useful during financial periods to maintain coherence in financial reporting. By establishing clear cut-off points, companies can better manage their inventory flow and ensure that all transactions are accounted for within the appropriate accounting period. This clarity is essential for stakeholders who rely on accurate financial statements to make informed decisions.
Analyzing Finished Goods Costs
Understanding the costs associated with finished goods is vital for setting pricing strategies and evaluating profitability. Regular audits help assess these costs accurately and ensure they align with overall business goals. Additionally, a thorough analysis can reveal insights into production efficiencies and potential areas for cost reduction, enabling businesses to adjust their pricing models in response to market changes. By keeping a close eye on finished goods costs, companies can remain competitive while maximizing their profit margins.
Evaluating Freight Costs
Freight costs can significantly impact overall inventory management. During an audit, companies should evaluate freight expenses related to shipping and receiving inventory to identify areas for cost reduction. This evaluation can uncover opportunities for negotiating better rates with carriers or optimizing shipping routes, ultimately leading to lower expenses. Moreover, understanding freight costs in relation to inventory turnover can help businesses make more informed decisions about stock levels and purchasing strategies.
Assessing Overhead Costs
Overhead costs, including storage and handling, should also be examined during inventory audits. Identifying inefficiencies in these areas can lead to cost savings and improved operational performance. For instance, businesses may find that certain storage methods are more costly than others, prompting a reevaluation of their warehousing strategies. Additionally, analyzing overhead costs can help in forecasting future expenses and budgeting more accurately, ensuring that resources are allocated wisely.
Reconciling Inventory Items
Reconciliation involves comparing physical counts with the inventory management system to resolve discrepancies. The process is crucial for minimizing variances and ensuring accurate financial reporting. Regular reconciliation not only helps maintain inventory accuracy but also fosters accountability among staff responsible for inventory management. By implementing routine checks and balances, businesses can cultivate a culture of diligence and responsibility, ultimately enhancing overall inventory control.
Matching Inventory Items
Matching inventory items involve ensuring that all records, receipts, and inventories correspond accurately. This step is paramount to maintaining the integrity of the inventory management system. Discrepancies can lead to significant financial implications, including overstocking or stockouts, which can disrupt operations and affect customer satisfaction. By establishing robust matching protocols, companies can mitigate these risks and ensure that their inventory data remains reliable and actionable.
In addition to these steps, leveraging technology can significantly enhance the inventory auditing process. Utilizing advanced inventory management software can automate many of the tasks involved, reducing human error and increasing efficiency. Furthermore, integrating real-time data analytics can provide deeper insights into inventory trends, enabling businesses to make proactive adjustments rather than reactive ones. This technological support not only streamlines the auditing process but also empowers organizations to respond swiftly to market demands and operational challenges.