Essential Guide to Effective Bill of Materials Inventory Management
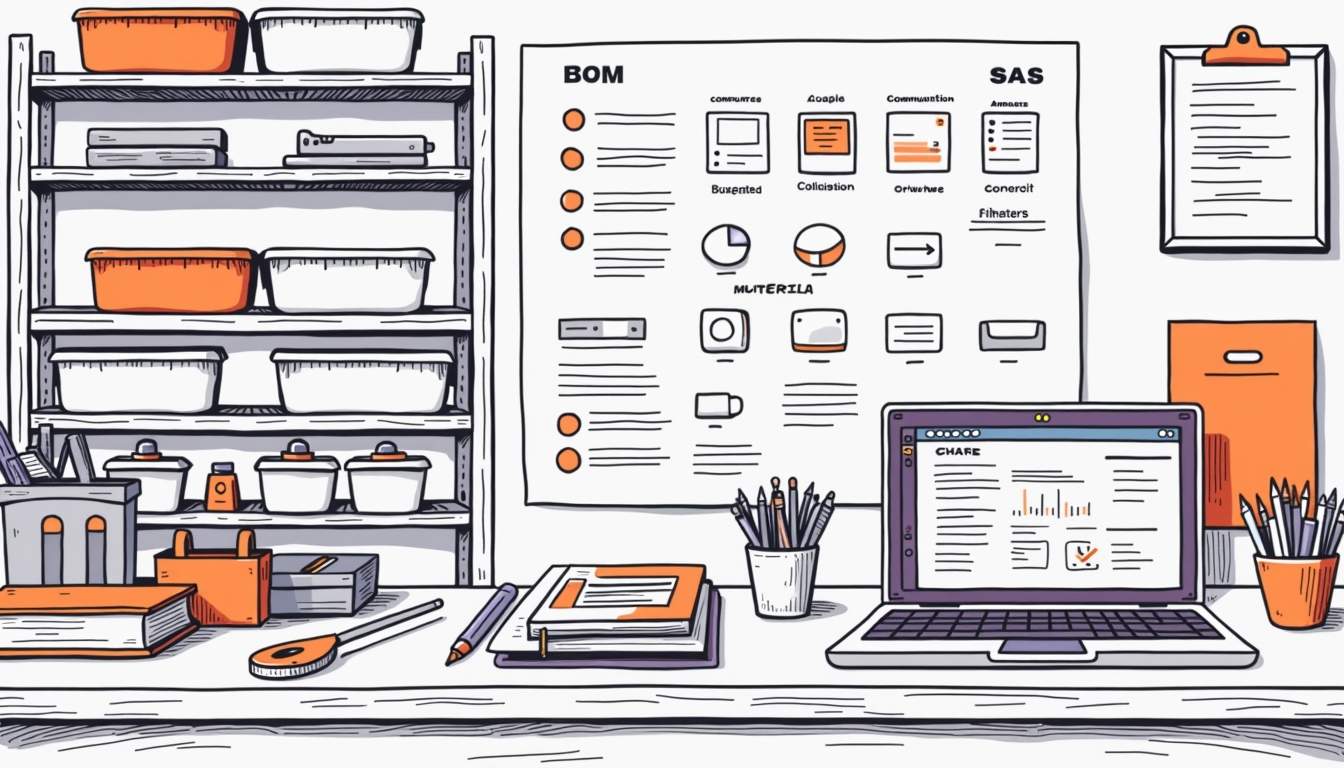
In today's fast-paced manufacturing landscape, efficient management of materials is critical to maintaining competitiveness and ensuring customer satisfaction. One essential component of this process is the Bill of Materials (BOM). This guide delves into effective BOM inventory management, highlighting key features, integration options, practical applications, and much more.
Overview
At its core, a Bill of Materials is a comprehensive list of raw materials, components, assemblies, and sub-assemblies required to manufacture a product. The BOM serves as a foundational document that guides the manufacturing process, ensuring that all necessary materials are accounted for and ready for production. This document is crucial not just for the manufacturing team, but also for various departments including procurement, inventory management, and even sales, as it provides a clear blueprint of what is needed to bring a product to life.
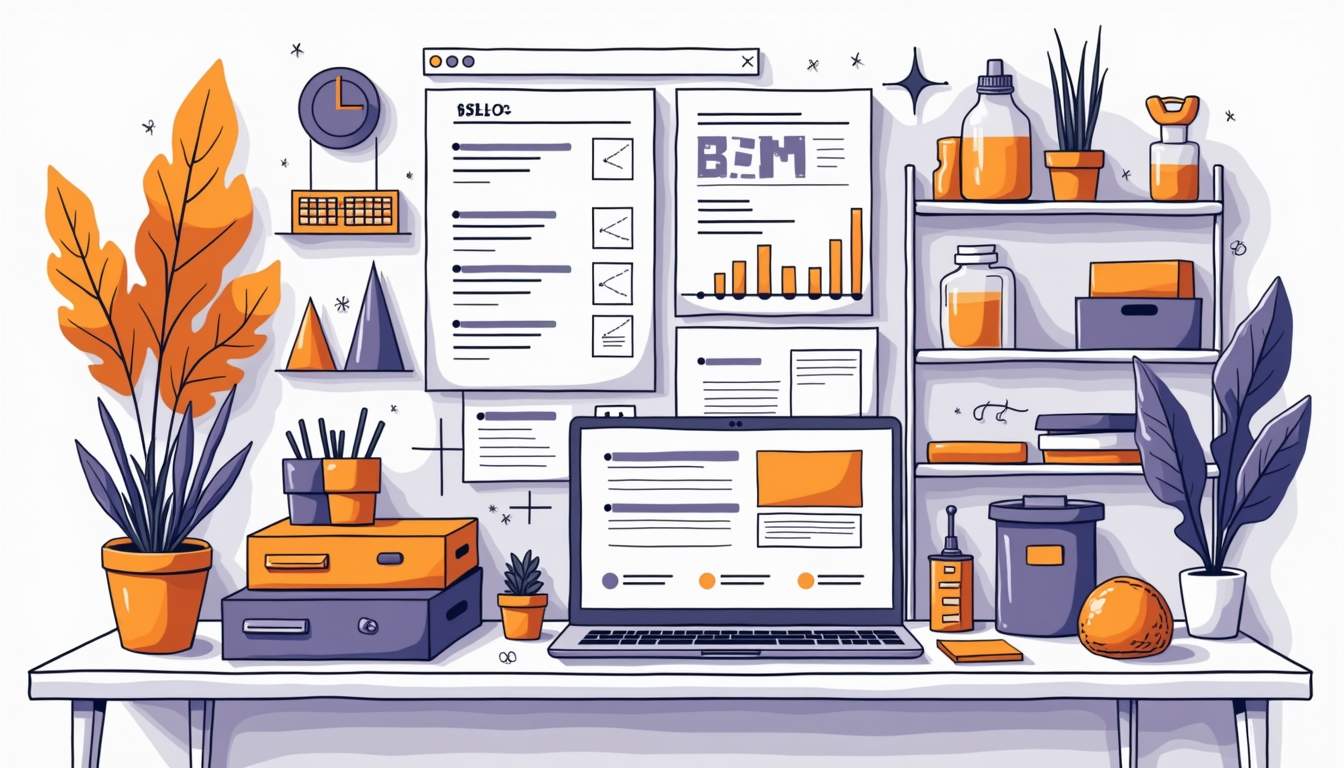
Effective BOM inventory management involves not only maintaining accurate records but also streamlining procurement, controlling costs, and optimizing production schedules. With the right approach, companies can reduce errors, improve efficiency, and enhance overall productivity. Furthermore, a well-structured BOM can facilitate better communication across departments, allowing teams to collaborate more effectively and respond swiftly to changes in demand or supply chain disruptions. By integrating advanced software solutions, organizations can automate updates to the BOM, ensuring that all stakeholders have access to real-time information, which is essential in today’s fast-paced manufacturing environment.
Moreover, the complexity of modern products often necessitates multi-level BOMs, where each assembly can have its own sub-assemblies and components. This hierarchical structure not only provides clarity but also aids in troubleshooting and maintenance, as it allows manufacturers to pinpoint exactly where a problem may arise in the production process. Additionally, a well-maintained BOM can play a vital role in regulatory compliance, as it provides a transparent record of all materials used, which is particularly important in industries such as aerospace, automotive, and pharmaceuticals, where safety and quality standards are paramount.
In the digital age, the integration of BOMs with other enterprise systems, such as ERP (Enterprise Resource Planning) and PLM (Product Lifecycle Management), has become increasingly important. This integration allows for seamless data flow between departments, ensuring that changes in design or material specifications are instantly reflected across all systems. As a result, companies can achieve greater agility in their operations, respond to market changes more effectively, and ultimately deliver higher-quality products to their customers. The evolution of BOM management continues to shape the future of manufacturing, making it an essential focus for organizations aiming to stay competitive in a rapidly changing landscape.
Key Features
Effective BOM inventory management systems include several key features that facilitate streamlined operations. Some of these features are:
- Real-time Tracking: Allows for monitoring inventory levels continuously, ensuring that any discrepancies can be addressed promptly.
- Version Control: Essential for tracking changes in BOM documents, especially when modifications occur due to design changes or supplier updates.
- Supplier Management: Streamlines communication with suppliers and helps track lead times and costs associated with components.
- Reporting Capabilities: Provides insights into inventory usage, cost analysis, and overall efficiency, allowing for informed decision-making.
By incorporating these features, organizations can achieve a higher level of BOM management, improving both operational efficiencies and bottom-line results. Additionally, effective BOM systems often include integration capabilities with other enterprise systems, such as ERP and PLM software. This integration ensures that data flows seamlessly across departments, reducing the likelihood of errors and enhancing collaboration among teams. For instance, engineering teams can access real-time inventory data while designing new products, allowing them to make informed decisions about materials and components early in the design process.
Furthermore, many modern BOM management systems leverage advanced technologies such as artificial intelligence and machine learning. These technologies can analyze historical data to predict future inventory needs, helping organizations to optimize stock levels and reduce excess inventory. By anticipating demand fluctuations, companies can minimize waste and improve their overall supply chain agility. This proactive approach not only enhances operational efficiency but also contributes to sustainability efforts by reducing the environmental impact associated with overproduction and waste.
Integration Options
Integrating BOM management systems with other business tools is crucial for maximizing functionality. Many organizations benefit from linking their BOM systems with:
- Enterprise Resource Planning (ERP) Systems: This integration allows for seamless data sharing between BOM and financial or manufacturing management systems.
- Computer-Aided Design (CAD) Software: Facilitates automatic updates to the BOM whenever design changes are made.
- Inventory Management Systems: Ensures materials are available when needed, reducing delays and production interruptions.
- Supply Chain Management Tools: Helps manage supplier relationships and streamline procurement processes.
By selecting the right integration options, businesses can significantly enhance their BOM management capabilities, leading to better inventory oversight and reduced operational costs. Furthermore, integrating with Customer Relationship Management (CRM) systems can provide valuable insights into customer preferences and trends, allowing for more accurate forecasting and product development. This holistic approach not only improves internal processes but also aligns production with market demand, ensuring that companies remain competitive.
Additionally, leveraging cloud-based integration solutions can offer increased flexibility and scalability. With cloud technology, organizations can access their BOM data from anywhere, facilitating real-time collaboration among teams, whether they are in the office or working remotely. This can be particularly beneficial for companies with multiple locations or those that operate in a global market, as it enables consistent updates and communication across various departments and regions, ultimately driving innovation and efficiency in product development.
Practical Use Cases
The practical application of BOM inventory management is vast and can be tailored to various industries. Here are some notable use cases:
- Manufacturing: In manufacturing sectors, an accurate BOM helps regulate inventory, ensuring that all components are available for assembly lines.
- Aerospace: The aerospace industry often relies on complex BOMs to meet stringent regulatory requirements and maintain safety standards.
- Electronics: BOM management systems streamline the production process by tracking numerous small components essential for electronic devices.
- Food and Beverage: Accurate BOMs ensure compliance with health regulations by maintaining detailed records of all ingredients used in products.
These applications underscore the versatility of BOM management across various fields, demonstrating its critical role in enhancing efficiency and compliance. Additionally, the automotive industry exemplifies the importance of BOMs, where intricate assemblies and thousands of parts must be meticulously documented. A well-structured BOM allows manufacturers to optimize their supply chain, reduce lead times, and improve overall production efficiency, which is vital in a highly competitive market.
Furthermore, the construction industry also benefits significantly from effective BOM management. In this sector, a comprehensive BOM is essential for project planning and cost estimation, as it details every material and component required for building projects. By utilizing BOMs, construction managers can ensure that materials are ordered in a timely manner, minimizing delays and cost overruns. This meticulous planning not only enhances project efficiency but also contributes to sustainability efforts by reducing waste through precise material management.
Industry Applications
BOM inventory management extends its benefits across multiple industries, each with unique requirements. Key industries include:
- Automotive: BOMs help manage parts inventory and supplier coordination, promoting just-in-time manufacturing strategies.
- Pharmaceutical: Precise BOMs are crucial for tracking ingredient sourcing, compliance, and production processes.
- Construction: In construction, BOMs help manage materials for various projects, ensuring timely deliveries and reducing waste.
Efficient BOM management tailored to these industry nuances allows businesses to align their operations with specific market demands and regulations.
In the automotive sector, the complexity of modern vehicles necessitates a detailed BOM that includes not only the individual parts but also their specifications, compatibility, and sourcing details. This level of detail aids manufacturers in maintaining quality control and minimizing production delays. Moreover, as electric vehicles gain traction, BOMs are adapting to include new components such as batteries and electronic systems, further complicating inventory management but also offering opportunities for innovation.
Similarly, in the pharmaceutical industry, the BOM process is integral to ensuring that all components meet stringent regulatory standards. This includes not only the active ingredients but also excipients and packaging materials. The ability to trace each component back to its source is vital for compliance with health regulations and for maintaining the integrity of the supply chain. As the industry moves towards more personalized medicine, the BOM will become even more critical in managing the diverse range of formulations and components required for tailored therapies.
Understanding the Bill of Materials (BOM)
To effectively manage BOM inventory, it’s essential to comprehend what a BOM entails. A Bill of Materials can be seen as the recipe for manufacturing products. It lists everything that goes into a finished product and often includes details such as:
- Item numbers associated with components and materials
- Quantities needed for each item
- Descriptions that clearly define each component to minimize confusion
- Units of measure (e.g., pieces, kilograms) for effective inventory tracking
Understanding these elements is fundamental, as they significantly impact inventory efficiency and production scheduling.
Moreover, a well-structured BOM not only facilitates smoother production processes but also enhances communication across various departments, such as engineering, procurement, and manufacturing. For instance, when engineers design a new product, they rely on the BOM to ensure that all necessary materials are available and that the specifications meet quality standards. This collaborative approach helps prevent costly delays and errors that can arise from miscommunication or incomplete information.
Additionally, BOMs can vary in complexity depending on the nature of the product being manufactured. For simple products, a single-level BOM may suffice, listing all components directly used in the final assembly. However, for more intricate products, multi-level BOMs are often employed, which break down assemblies into sub-assemblies and components. This hierarchical structure allows manufacturers to gain a clearer understanding of the relationships between various parts, enabling better planning and resource allocation throughout the production cycle.
Why a BOM Matters
The importance of a BOM cannot be overstated. A well-structured Bill of Materials lays the groundwork for successful manufacturing operations. Reasons why a BOM is critical include:
- Cost Control: Helps manage expenses by keeping clear records of materials and quantities needed.
- Production Efficiency: Facilitates smooth workflows by ensuring all necessary components are on hand and reducing downtime.
- Quality Assurance: Ensures that the correct materials are used in production, reducing the likelihood of defects.
Ultimately, a solid BOM is foundational for building reliable and effective manufacturing processes, directly impacting profitability and customer satisfaction. Moreover, a BOM serves as a vital communication tool among various teams, including engineering, procurement, and production. By providing a clear and detailed outline of the materials required, it helps align all stakeholders on project specifications and timelines, reducing the risk of misunderstandings that can lead to costly delays.
In addition, the BOM can be instrumental in inventory management. By accurately forecasting the materials needed for production, businesses can optimize their inventory levels, minimizing excess stock and associated carrying costs. This not only streamlines operations but also enhances the ability to respond quickly to market demands. As industries increasingly adopt just-in-time manufacturing practices, the role of a BOM in maintaining agility and responsiveness in supply chains becomes even more critical.
Forecasting BOM Inventory Needs
Accurate forecasting of BOM inventory needs is a pivotal factor in maintaining operational efficiency. It provides insight into future demand and helps in planning inventory levels proactively. Techniques that organizations can adopt include:
- Historical Analysis: Reviewing past sales and production data can yield accurate predictions on future material requirements.
- Seasonal Trends: Recognizing patterns within specific seasons allows companies to adjust inventory accordingly.
- Market Research: Keeping track of changes in market demand can help anticipate shifts in volume and accordingly adjust BOM needs.
By carefully forecasting inventory requirements, businesses can avoid overstocking and stockouts, both of which can severely impact operations. Moreover, accurate forecasting not only optimizes inventory levels but also enhances cash flow management, allowing firms to allocate resources more effectively. For instance, when a company can predict an increase in demand for a particular product line, it can ramp up production schedules and ensure that the necessary materials are on hand, thus preventing delays that could frustrate customers and damage the brand's reputation.
Additionally, leveraging advanced technologies such as machine learning and artificial intelligence can significantly enhance forecasting accuracy. These tools analyze vast amounts of data, identifying complex patterns and correlations that may not be immediately apparent through traditional methods. By integrating these technologies into their inventory management systems, businesses can achieve a more agile response to market fluctuations, ensuring they remain competitive in an ever-evolving landscape. This proactive approach to BOM inventory forecasting not only streamlines operations but also fosters a culture of continuous improvement within the organization.
Streamlining BOM Inventory Management
Streamlining BOM inventory management involves utilizing best practices to improve efficiency. Recommendations include:
- Centralized Data Management: Maintain all BOM data in a single accessible platform to reduce errors and improve accessibility.
- Regular Updates: Schedule routine reviews of the BOM to reflect changes in materials and supplier information.
- Employee Training: Investing in training ensures that team members understand the BOM management system and its processes.
Implementing these practices helps foster a culture of efficiency and accountability within the organization. Moreover, integrating advanced technologies such as cloud-based solutions can further enhance BOM management. Cloud platforms not only provide real-time access to data but also facilitate collaboration among various departments, ensuring that everyone is on the same page regarding inventory levels and material requirements. This interconnectedness can significantly reduce lead times and improve overall responsiveness to market demands.
Additionally, leveraging analytics tools can provide valuable insights into inventory trends and usage patterns. By analyzing historical data, organizations can make informed decisions about stock levels, anticipate shortages, and optimize reorder points. This proactive approach not only minimizes excess inventory but also helps in maintaining a lean supply chain, ultimately leading to cost savings and improved profitability. Embracing these strategies can transform BOM management from a reactive process into a strategic advantage for the business.
Advantages of Automated BOM Management
Automating BOM management offers many benefits that can transform operations. Key advantages include:
- Increased Accuracy: Automation minimizes manual entry errors, ensuring data integrity.
- Time Savings: Reduces administrative workload, allowing staff to focus on more strategic tasks.
- Enhanced Collaboration: Cloud-based solutions enable real-time collaboration across departments and locations.
Ultimately, automation can lead to significant improvements in productivity and operational efficiency. Additionally, automated BOM management systems can provide comprehensive version control, ensuring that all stakeholders are working with the most current data. This is particularly crucial in industries where product specifications frequently change, as it helps to prevent costly mistakes that can arise from using outdated information. By maintaining a single source of truth, teams can streamline their workflows and reduce the time spent on reconciling discrepancies.
Moreover, automated systems often come equipped with advanced analytics capabilities, allowing organizations to gain insights into their manufacturing processes. By analyzing BOM data, companies can identify trends, forecast material needs, and optimize inventory levels, which can lead to reduced carrying costs and improved cash flow. With the ability to quickly adapt to market demands and production schedules, businesses can enhance their competitiveness and responsiveness in an ever-evolving landscape.
Enhance BOM Management with Automation Tools
Utilizing specific automation tools can further optimize BOM management. Some recommended tools include:
- Cloud-Based BOM Management Software: These solutions facilitate real-time updates and access for all team members, ensuring that everyone is on the same page and reducing the risk of errors associated with outdated information.
- Inventory Management Systems: Integrate with BOMs to ensure alignment between materials on hand and what is required, allowing for better control over stock levels and minimizing excess inventory costs.
- Forecasting Tools: Use advanced analytics to predict future inventory needs, enhancing responsiveness to market changes and enabling proactive decision-making to meet customer demands.
Implementing these tools can significantly streamline BOM processes and enhance overall efficiency. Additionally, automating BOM management can lead to improved collaboration across departments, as stakeholders can access and share critical information seamlessly. For instance, engineering teams can quickly update specifications, while procurement can adjust orders based on the latest data, fostering a more agile and responsive workflow.
Moreover, the integration of automation tools can also provide valuable insights through data analytics. By analyzing historical data and trends, organizations can identify patterns that inform better planning and forecasting. This not only helps in optimizing inventory levels but also aids in reducing lead times and improving supplier relationships. As companies increasingly embrace digital transformation, leveraging these automation solutions becomes essential for maintaining a competitive edge in today's fast-paced market.
Additional Resources
To further assist in understanding and implementing effective BOM inventory management, consider exploring the following resources:
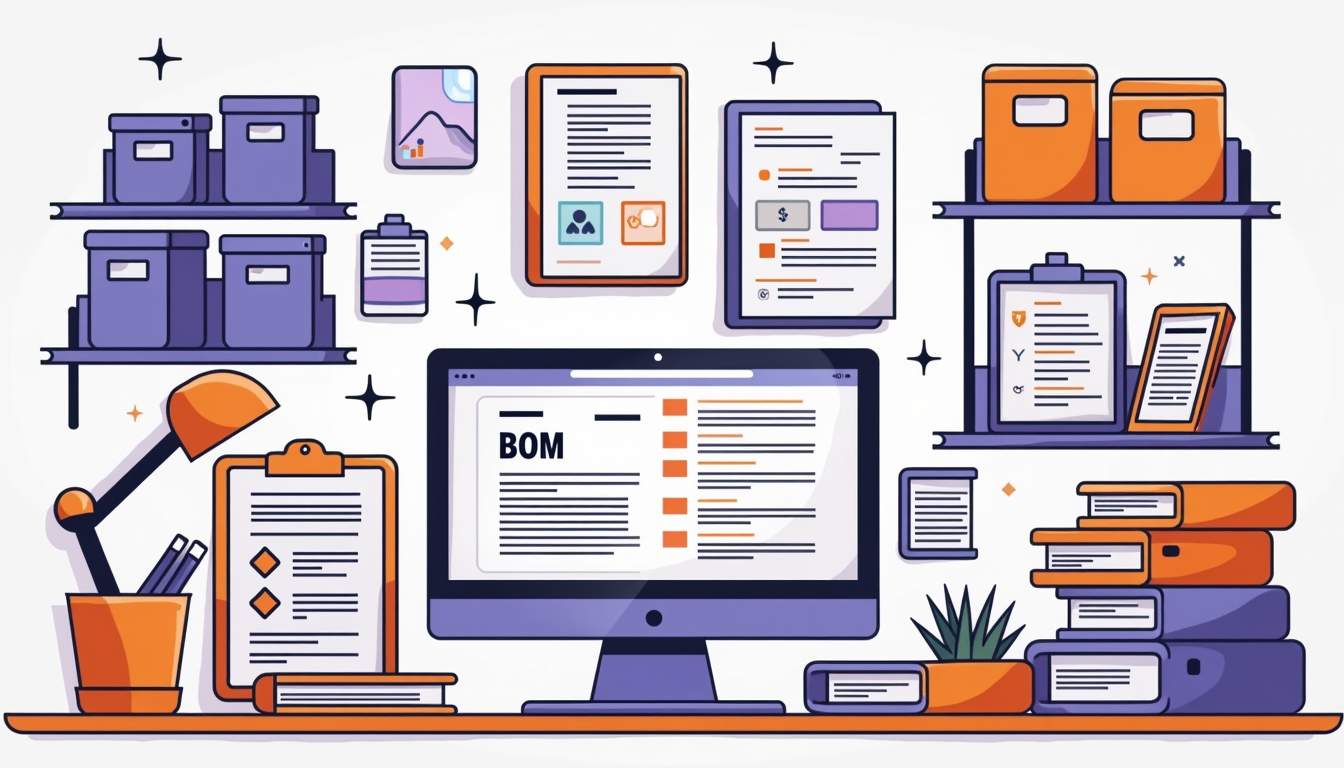
Essential Requirements for Inventory Management Systems
Any chosen inventory management system should encompass crucial components like tracking capabilities, reporting features, and user-friendly interfaces to ensure seamless operations. Additionally, integration with other business systems, such as ERP and CRM platforms, can significantly enhance the functionality of the inventory management system, allowing for real-time data sharing and improved decision-making. A robust inventory management system should also offer customizable alerts and notifications to keep teams informed about stock levels, reorder points, and potential discrepancies, thereby minimizing the risk of stockouts or overstock situations.
A Quick Guide to B2B Inventory Management
Understanding the intricacies of B2B inventory management can help businesses maintain robust supply chains and satisfy customer demands efficiently. This involves not only managing stock levels but also developing strong relationships with suppliers and distributors. Implementing strategies such as just-in-time inventory can reduce holding costs while ensuring that products are available when needed. Moreover, leveraging technology like RFID and barcode scanning can streamline the tracking process, providing businesses with greater visibility and control over their inventory flows.
Understanding Inventory Revaluation and Its Benefits
Learning about inventory revaluation can aid organizations in maintaining accurate financial records, reflecting the true value of their inventory. This process is particularly important during periods of market volatility, where fluctuations in material costs can significantly impact a company's bottom line. By regularly assessing and adjusting inventory values, businesses can make more informed financial decisions, optimize their pricing strategies, and ultimately enhance profitability. Additionally, understanding the implications of inventory revaluation on tax liabilities and financial reporting can help organizations stay compliant and avoid potential pitfalls.
Creating an Inventory Management System Using Excel
While many robust systems exist, a simple Excel spreadsheet can serve as a valuable tool for smaller operations looking to manage their BOM effectively. Excel offers flexibility and ease of use, allowing users to customize their inventory tracking according to specific needs. By utilizing features such as pivot tables, conditional formatting, and data validation, businesses can create a dynamic and interactive inventory management system. Moreover, incorporating formulas for automatic calculations can save time and reduce errors, making it easier to analyze trends and forecast future inventory needs.
In addition to these resources, exploring case studies and industry reports can provide valuable insights into how other organizations have successfully implemented BOM inventory management strategies. Engaging in forums or online communities dedicated to inventory management can also foster knowledge sharing and provide practical advice from experienced professionals in the field. As technology continues to evolve, staying updated on the latest trends and tools in inventory management will empower businesses to remain competitive and responsive to market demands.