How a Bill of Materials (BOM) Can Streamline Your E-Commerce Supply Chain
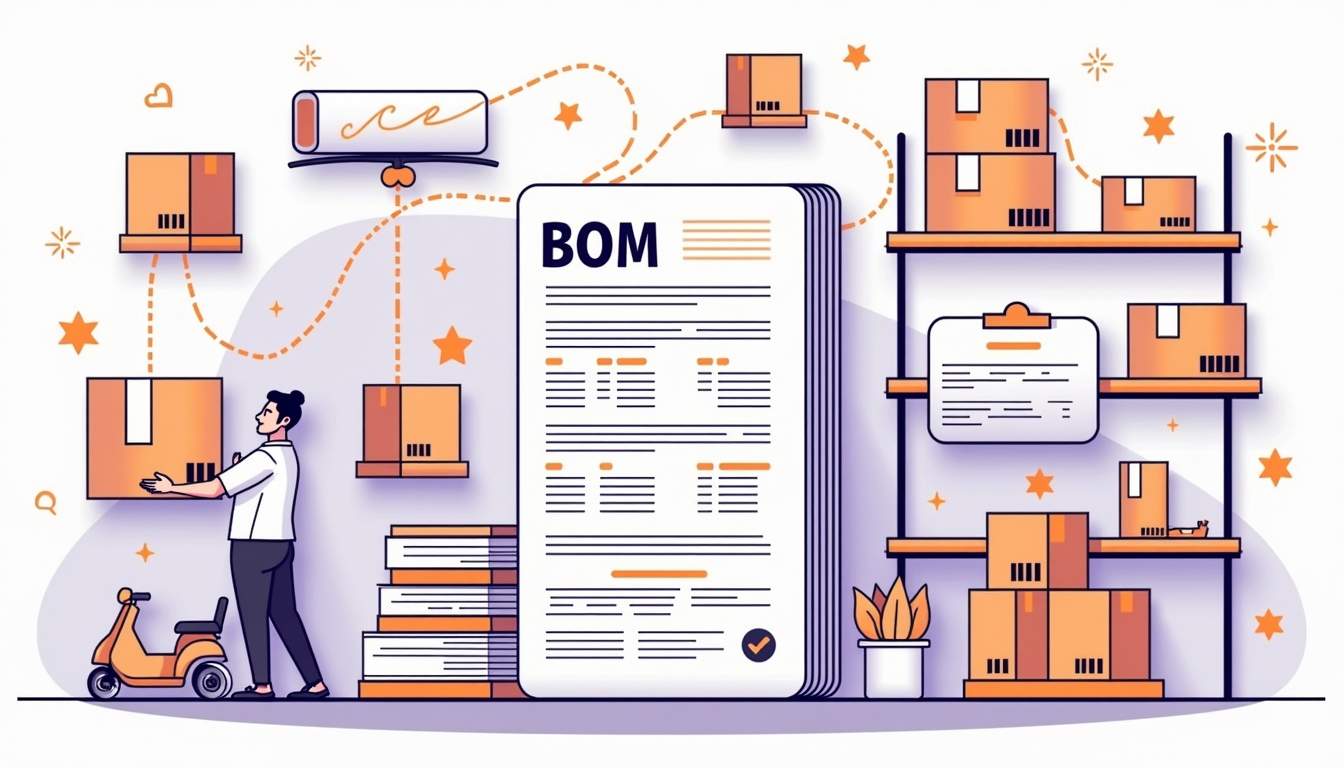
In the fast-paced world of e-commerce, efficiency and accuracy are crucial to maintaining a competitive edge. One of the most effective tools for achieving this is a Bill of Materials (BOM). A BOM is a comprehensive list of raw materials, components, and instructions required to construct, manufacture, or repair a product or service. By integrating a BOM into your e-commerce supply chain, you can streamline operations, reduce errors, and enhance productivity. Let's explore how a BOM can transform your supply chain processes and optimize your business operations.
Understanding the Basics of a Bill of Materials (BOM)
What is a Bill of Materials?
A Bill of Materials is essentially a detailed inventory of all the parts, components, and assemblies needed to create a product. It serves as a blueprint for product creation, detailing everything from raw materials to subassemblies. This document is crucial for manufacturers and suppliers as it ensures that all necessary components are available and accounted for during the production process.
In the context of e-commerce, a BOM can be used to manage inventory levels, forecast demand, and streamline the procurement process. By having a clear understanding of what is needed to produce each product, businesses can avoid overstocking or understocking, which can lead to increased costs and customer dissatisfaction.
Types of BOMs
There are several types of BOMs, each serving different purposes. The most common types include the Engineering BOM (EBOM), Manufacturing BOM (MBOM), and Sales BOM (SBOM). An EBOM is used during the design phase and includes all the technical specifications. An MBOM is used during the manufacturing process and includes all the materials required for production. An SBOM, on the other hand, is used for sales and includes all the items that are sold as part of a product.
Understanding the different types of BOMs is essential for e-commerce businesses, as it allows them to choose the right type of BOM for their specific needs. This ensures that all aspects of the supply chain are aligned and working towards the same goal.
Benefits of Implementing a BOM in Your E-Commerce Supply Chain
Improved Inventory Management
One of the primary benefits of using a BOM is improved inventory management. By having a detailed list of all the components needed for each product, businesses can better manage their inventory levels. This reduces the risk of stockouts and overstocking, which can lead to increased costs and lost sales.

With a BOM, businesses can also forecast demand more accurately. By understanding the components needed for each product, businesses can predict which products will be in high demand and adjust their inventory levels accordingly. This ensures that they are always prepared to meet customer demand, leading to increased customer satisfaction and loyalty.
Enhanced Production Efficiency
A BOM can also enhance production efficiency by providing a clear roadmap for the manufacturing process. By having a detailed list of all the components needed for each product, businesses can streamline their production processes and reduce the risk of errors. This leads to faster production times and increased productivity.
In addition, a BOM can help businesses identify potential bottlenecks in their production processes. By analyzing the components needed for each product, businesses can identify areas where they may be experiencing delays or inefficiencies and take steps to address these issues. This leads to a more efficient and streamlined production process.
Cost Reduction
Another significant benefit of using a BOM is cost reduction. By having a detailed list of all the components needed for each product, businesses can better manage their procurement processes and reduce the risk of overordering or underordering materials. This leads to reduced costs and increased profitability.
In addition, a BOM can help businesses identify cost-saving opportunities. By analyzing the components needed for each product, businesses can identify areas where they may be able to reduce costs, such as by sourcing materials from different suppliers or using alternative materials. This leads to increased cost savings and improved profitability.
How to Implement a BOM in Your E-Commerce Supply Chain
Step 1: Define Your Products and Components
The first step in implementing a BOM is to define your products and components. This involves creating a detailed list of all the products you sell and the components needed to create each product. This list should include everything from raw materials to subassemblies and should be as detailed as possible.
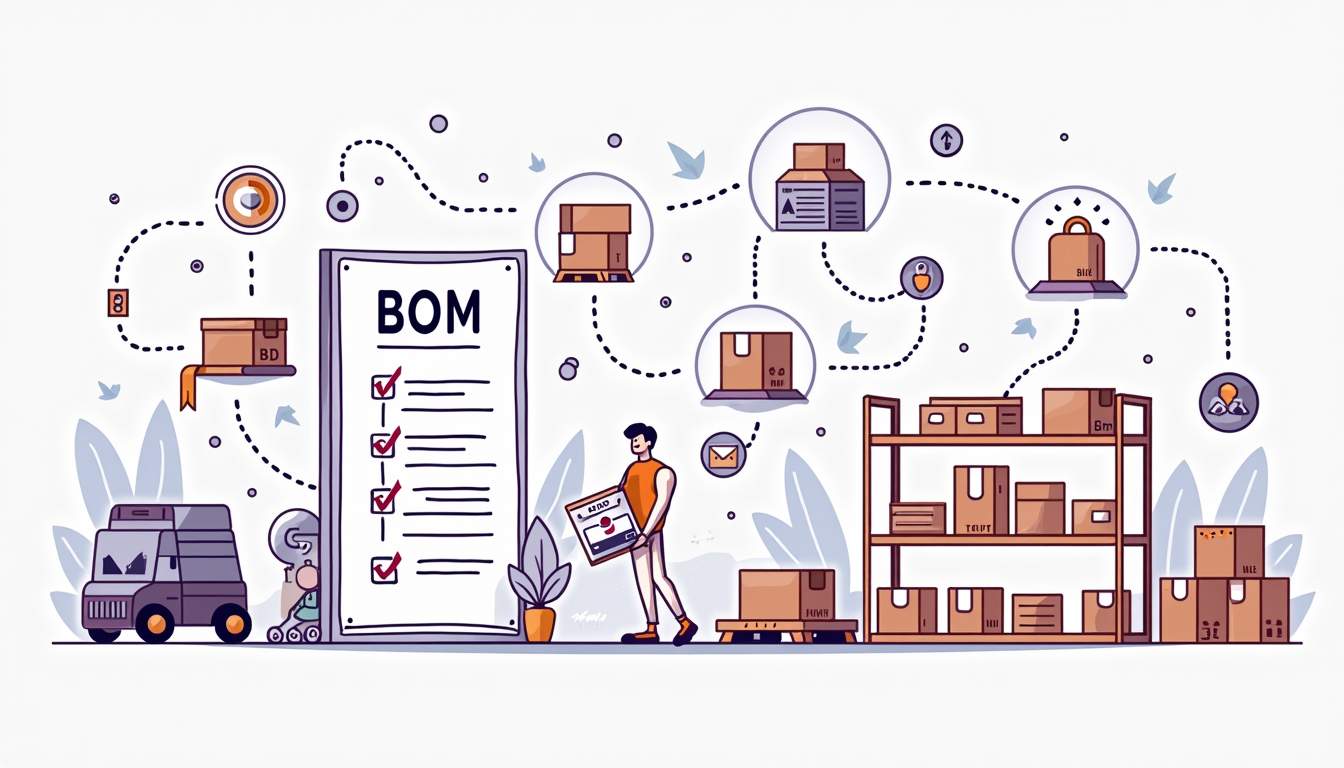
Once you have defined your products and components, you can begin to create your BOM. This involves organizing your list of components into a structured format that can be easily understood and used by your team. This may involve creating a spreadsheet or using specialized software to manage your BOM.
Step 2: Choose the Right BOM Software
Choosing the right BOM software is crucial to the success of your implementation. There are many different types of BOM software available, each with its own features and capabilities. When choosing a BOM software, consider factors such as ease of use, integration with your existing systems, and scalability.
Once you have chosen your BOM software, you can begin to input your product and component data into the system. This may involve importing data from existing spreadsheets or manually entering data into the system. Once your data is in the system, you can begin to use your BOM to manage your inventory, forecast demand, and streamline your production processes.
Step 3: Train Your Team
Training your team is an essential step in implementing a BOM. Your team will need to understand how to use the BOM software and how to interpret the data it provides. This may involve providing training sessions or creating user guides and documentation to help your team get up to speed.
Once your team is trained, you can begin to use your BOM to streamline your supply chain processes. This may involve using the BOM to manage your inventory levels, forecast demand, and optimize your production processes. By using your BOM effectively, you can achieve significant improvements in efficiency and productivity.
Challenges and Considerations
Data Accuracy and Maintenance
One of the key challenges in implementing a BOM is ensuring data accuracy and maintenance. A BOM is only as good as the data it contains, so it's crucial to ensure that all data is accurate and up-to-date. This may involve regularly reviewing and updating your BOM to ensure that it reflects any changes in your products or components.
In addition, it's important to have a process in place for maintaining your BOM. This may involve assigning responsibility for maintaining the BOM to a specific team or individual and establishing regular review and update processes to ensure that your BOM remains accurate and up-to-date.
Integration with Existing Systems
Integrating your BOM with your existing systems can also be a challenge. Your BOM will need to integrate with your existing inventory management, procurement, and production systems to be effective. This may involve working with your IT team or software vendors to ensure that your BOM software is compatible with your existing systems.
Once your BOM is integrated with your existing systems, you can begin to use it to streamline your supply chain processes. This may involve using your BOM to manage your inventory levels, forecast demand, and optimize your production processes. By integrating your BOM with your existing systems, you can achieve significant improvements in efficiency and productivity.
Scalability and Flexibility
Another consideration when implementing a BOM is scalability and flexibility. Your BOM will need to be scalable to accommodate changes in your product offerings or production processes. This may involve choosing a BOM software that can easily accommodate changes in your product or component data.
In addition, your BOM will need to be flexible to accommodate changes in your supply chain processes. This may involve regularly reviewing and updating your BOM to ensure that it reflects any changes in your products or components. By ensuring that your BOM is scalable and flexible, you can ensure that it remains effective as your business grows and evolves.
Conclusion
Implementing a Bill of Materials in your e-commerce supply chain can lead to significant improvements in efficiency, productivity, and cost savings. By providing a clear roadmap for the production process, a BOM can help businesses manage their inventory levels, forecast demand, and optimize their production processes. While there are challenges to implementing a BOM, such as ensuring data accuracy and integration with existing systems, the benefits far outweigh the challenges. By taking the time to implement a BOM effectively, businesses can achieve significant improvements in their supply chain processes and maintain a competitive edge in the fast-paced world of e-commerce.