Mastering the Total Manufacturing Cost Formula for Your Business
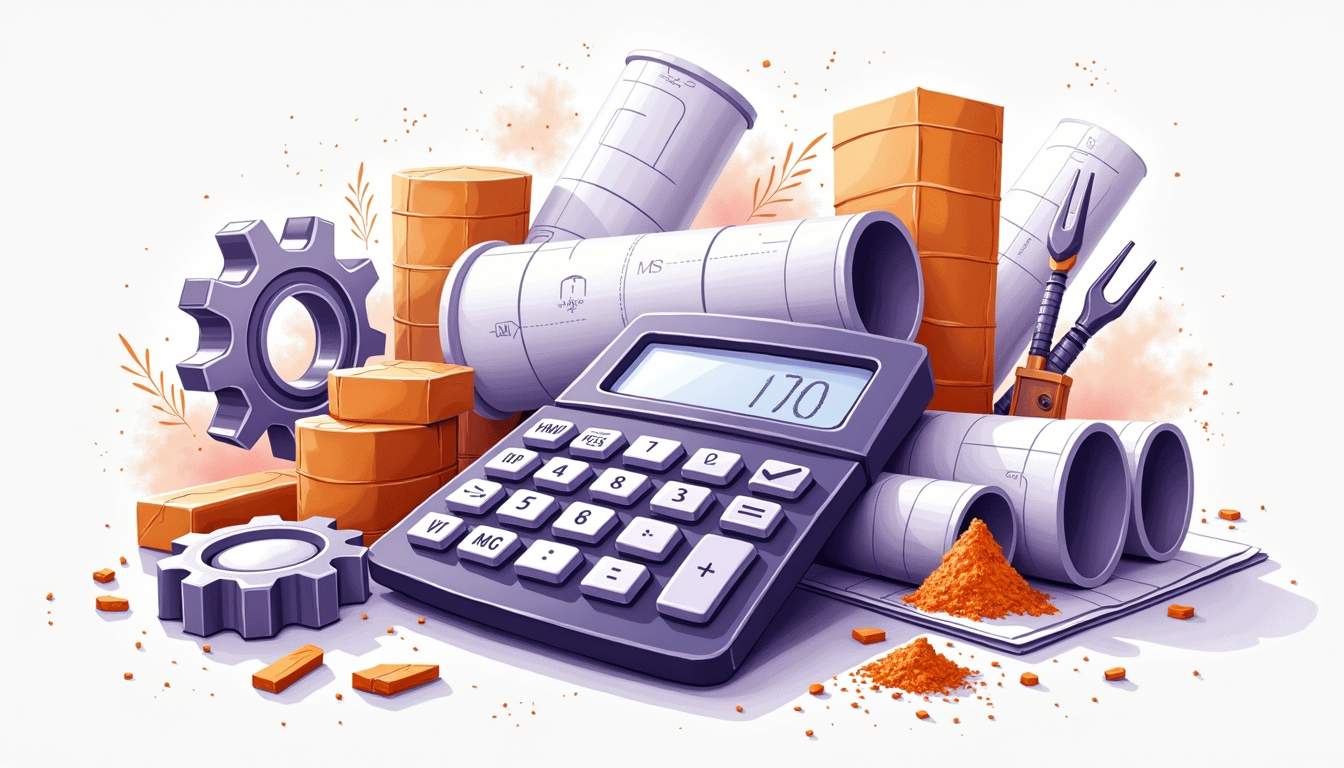
Understanding the total manufacturing cost (TMC) is essential for businesses involved in production. It not only determines pricing strategies but also helps in identifying cost-saving opportunities. This article delves into the total manufacturing cost formula, its components, and practical examples, ensuring that you can master this crucial aspect of your business operations.
Understanding the Total Manufacturing Cost Formula
The total manufacturing cost formula is a comprehensive calculation that encompasses all costs associated with the production of goods. This formula serves as a crucial tool for manufacturers, enabling them to determine the total expenses incurred during the manufacturing process. A solid grasp of this formula can lead to better budgeting, forecasting, and overall financial management.
The formula can be expressed as:
- Total Manufacturing Cost = Direct Materials + Direct Labor + Manufacturing Overhead
By breaking this down into its components, businesses can better understand how each element contributes to the overall cost structure.
Direct materials refer to the raw materials that are directly traceable to the finished product. For instance, in the furniture manufacturing industry, wood, fabric, and metal are considered direct materials. Understanding the fluctuations in material costs, influenced by market demand and supply chain issues, is vital for manufacturers. By effectively managing these costs, companies can identify opportunities for cost savings, negotiate better prices with suppliers, and even explore alternative materials that may offer similar quality at a lower price.
Direct labor, on the other hand, includes the wages and benefits paid to workers who are directly involved in the production process. This can range from assembly line workers to skilled craftsmen. Tracking direct labor costs is essential for maintaining productivity and efficiency in the manufacturing process. Manufacturers often invest in training programs to enhance the skills of their workforce, which can lead to increased output and reduced labor costs over time. Additionally, understanding labor costs helps in workforce planning and can inform decisions about automation and technology investments that may further streamline operations.
Defining Total Manufacturing Cost
Total manufacturing cost is a term that refers to the cumulative costs incurred in the process of producing goods. It combines various direct and indirect costs associated with production. Let’s take a closer look at the key components that make up this vital calculation.
Breakdown of Direct Materials
Direct materials include all raw materials and components that become a part of the finished product. These costs are easily attributable to the specific units produced. Managing direct materials effectively ensures that businesses can maintain quality while keeping costs in check. Monitoring prices and supplier relationships are critical strategies for managing direct material costs.
To optimize your spending on direct materials, consider evaluating bulk purchasing options or negotiating better terms with suppliers. This can lead to significant savings over time, ensuring that you maintain a competitive edge. Additionally, implementing a just-in-time inventory system can minimize storage costs and reduce waste, allowing for a more agile response to market demands.
Overview of Direct Labor
Direct labor refers to the cost of labor directly involved in the manufacturing process. This includes wages, bonuses, and benefits paid to workers who are actively engaged in producing goods. Understanding direct labor costs allows businesses to measure productivity and identify areas where efficiency can be improved.
Labor costs can fluctuate based on market conditions, skill levels, and workforce availability. Analyzing labor efficiency through performance metrics can provide insights into optimizing labor costs without compromising quality. Furthermore, investing in employee training and development can enhance skill sets, leading to higher productivity and reduced error rates in production, which ultimately contributes to lower overall costs.
Insights into Manufacturing Overhead
Manufacturing overhead encompasses all indirect costs associated with production that cannot be directly tied to specific units. This includes utilities, rent, depreciation, and salaries of supervisory and support staff. A clear understanding of manufacturing overhead is vital for effectively allocating costs to products and ensuring accurate pricing strategies.
To manage overhead costs, businesses should conduct regular audits of their production facilities and seek ways to streamline operations. Energy-efficient equipment and preventive maintenance programs are some strategies that can reduce overhead expenses while maintaining production quality. Additionally, leveraging technology such as automation and data analytics can provide deeper insights into operational efficiencies, helping to identify areas where costs can be further minimized without sacrificing output or quality.
The Total Cost Formula in Manufacturing Explained
The total cost formula in manufacturing is more than just a simple calculation. It represents a comprehensive view of all expenses involved in the production cycle. Understanding this formula allows manufacturers to establish pricing, analyze profitability, and develop strategic plans for growth. By consistently applying this formula, businesses can maintain a healthy financial standing and make informed decisions.
At its core, the total cost formula encompasses various components, including fixed costs, variable costs, and semi-variable costs. Fixed costs, such as rent and salaries, remain constant regardless of production levels, while variable costs fluctuate with output, including raw materials and direct labor. Semi-variable costs, on the other hand, contain both fixed and variable elements, such as utility bills that may have a base charge plus additional fees based on usage. By dissecting these costs, manufacturers gain insights into their operational efficiency and can identify areas for potential savings or investment.
Moreover, the total cost formula plays a crucial role in budgeting and forecasting within the manufacturing sector. By analyzing historical data and market trends, manufacturers can project future costs and revenues, allowing them to make proactive adjustments to their operations. This foresight is particularly important in an ever-evolving market where fluctuations in material prices or changes in consumer demand can significantly impact profitability. Additionally, understanding the total cost can help manufacturers negotiate better terms with suppliers, optimize inventory levels, and ultimately enhance their competitive edge in the industry.
Two Illustrative Examples of Total Manufacturing Costs
To clarify the total manufacturing cost concept, let’s explore two practical examples that illustrate how the formula works in real-world scenarios.
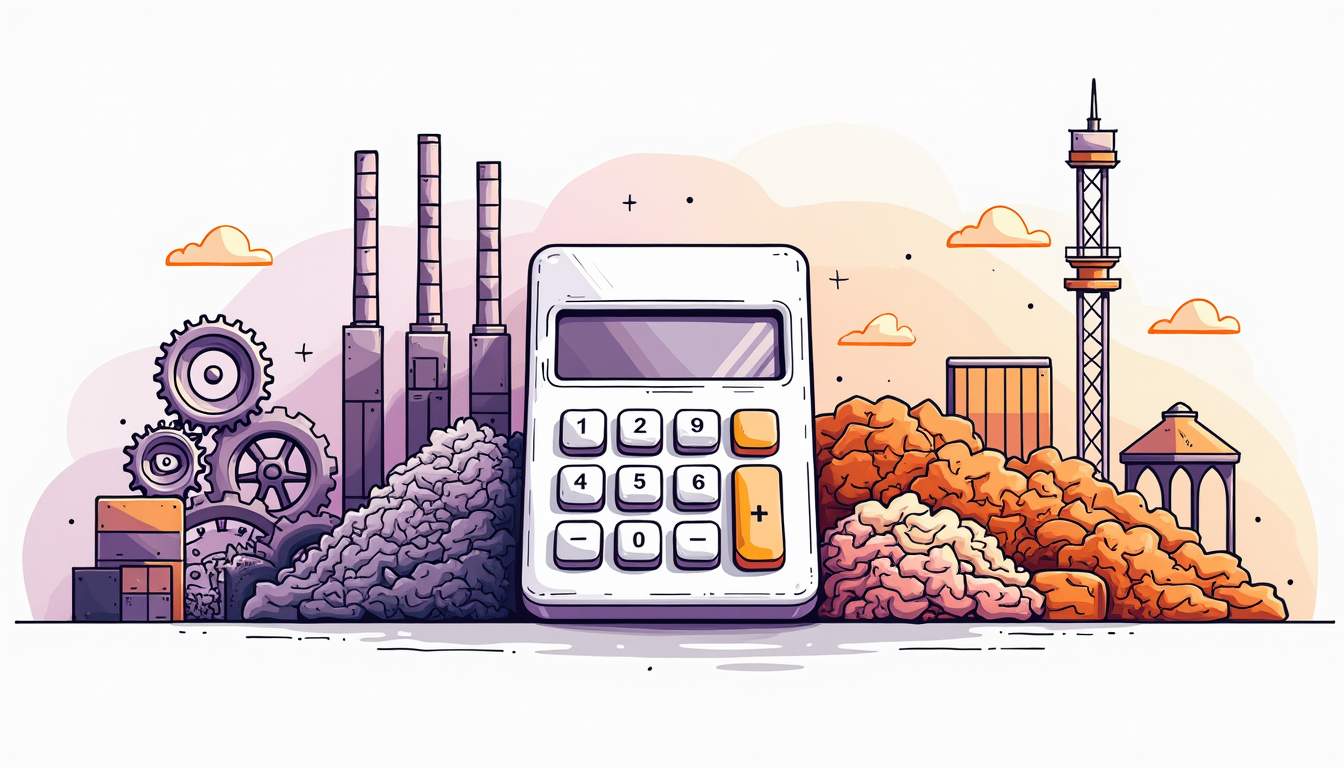
The first example involves a furniture manufacturer producing wooden tables. The direct materials cost includes wood, varnish, and nails, while direct labor covers the wages of carpenters. The production facility incurs overhead costs like electricity and maintenance for machinery. By collating all these costs, the manufacturer can yield the total manufacturing cost for a specific period. Additionally, the manufacturer may also consider the costs associated with quality control, which ensures that each table meets the desired standards before it reaches the customer. This could involve hiring inspectors or implementing testing procedures, further refining the understanding of total costs and their impact on pricing strategies.
The second example revolves around a clothing manufacturer. Here, direct materials would be fabric and thread, while direct labor takes into account the salaries of seamstresses. Overhead costs might include the leasing of factory space and equipment depreciation. Again, calculating the total manufacturing cost allows the business to price their products effectively and assess profitability. Moreover, in the clothing industry, factors such as seasonal trends and consumer demand can significantly influence production runs and inventory levels, which in turn affect the total manufacturing costs. For instance, if a manufacturer anticipates a surge in demand for a particular style, they may ramp up production, leading to bulk purchasing of materials that could reduce per-unit costs, showcasing the dynamic nature of manufacturing cost management.
Clarifying Total Manufacturing Cost
As we delve deeper into total manufacturing costs, it becomes evident that clarity and precision in understanding these costs are crucial. Small changes in any of the components can significantly impact the overall cost and profitability. This understanding is not just beneficial for internal accounting but also plays a vital role in pricing strategies and competitive positioning in the market.
Components of Direct Materials
Direct materials can vary greatly depending on the type of product being manufactured. It's essential to keep an inventory of these materials, monitor their prices, and maintain relationships with reliable suppliers. Keeping track of market trends can help in making better purchasing decisions and controlling these costs. Furthermore, leveraging technology such as inventory management software can streamline this process, providing real-time data on stock levels and supplier performance.
For many businesses, implementing a Just-In-Time (JIT) inventory system can further help in managing direct material costs. This approach minimizes excess inventory and reduces waste, contributing to a healthier bottom line. However, it requires a delicate balance; companies must ensure that their supply chain is robust enough to support this model, as any disruption can lead to production delays and increased costs. Additionally, fostering strong partnerships with suppliers can enhance flexibility and responsiveness in the JIT system.
Key Aspects of Direct Labor
Effective management of direct labor involves not just tracking hours worked but also investing in training and development. A well-trained workforce is not only more efficient but also leads to higher-quality products. Implementing performance-based incentives can also boost productivity, ensuring that labor costs translate into tangible benefits for the business. Moreover, creating a positive work environment can enhance employee morale, which is often reflected in their productivity levels and overall job satisfaction.
By utilizing technology, companies can enhance productivity tracking, establish performance benchmarks, and thus optimize direct labor costs in their manufacturing processes. Tools such as time-tracking software and workforce analytics can provide insights into labor utilization, helping managers identify bottlenecks and areas for improvement. Additionally, investing in automation for repetitive tasks can free up skilled labor for more complex operations, ultimately leading to a more efficient manufacturing process.
Exploring Manufacturing Overhead
Manufacturing overhead comprises many indirect costs, making it a challenge to manage. Regularly reviewing these costs can unveil opportunities for savings. For instance, energy audits can reveal possibilities for reducing utility expenses, while equipment assessments can identify opportunities for less costly alternatives or upgrades. Furthermore, implementing energy-efficient practices and technologies can not only lower overhead costs but also contribute to sustainability goals, enhancing the company’s reputation in the market.
Understanding fixed versus variable overhead costs can also provide insights into more strategic budgeting and planning, allowing businesses to allocate resources more effectively and improve overall productivity. By analyzing these costs in relation to production levels, companies can better forecast expenses and adjust their operations accordingly. This proactive approach helps in maintaining a competitive edge, especially in industries where profit margins are tight and efficiency is paramount.
The Total Cost Formula in Manufacturing
In the ever-evolving landscape of manufacturing, applying the total cost formula is more critical than ever. It is not only a tool for present operations but a framework for future planning. Identifying how costs function today will inform decisions that shape the direction and profitability of your manufacturing endeavors tomorrow.
Understanding the total cost formula involves a comprehensive analysis of both fixed and variable costs associated with production. Fixed costs, such as rent, salaries, and equipment depreciation, remain constant regardless of the production volume, while variable costs fluctuate with the level of output, including raw materials and labor. By meticulously tracking these costs, manufacturers can pinpoint inefficiencies and optimize their processes, leading to improved margins. Additionally, leveraging technology like ERP systems can facilitate real-time data analysis, allowing for more agile decision-making and strategic adjustments in response to market demands.
Moreover, the total cost formula extends beyond mere calculations; it encompasses the entire supply chain. Factors such as logistics, inventory management, and supplier relationships play a pivotal role in determining overall costs. For instance, optimizing transportation routes and reducing lead times can significantly lower costs, enhancing competitiveness in a global market. As manufacturers strive for sustainability, incorporating environmental costs into the total cost formula is becoming increasingly important. This holistic approach not only aids in compliance with regulations but also appeals to a growing consumer base that values eco-friendly practices, ultimately driving both brand loyalty and profitability.
Two Practical Examples of Manufacturing Costs
Let's look into two practical examples that highlight the implications of mastering the total manufacturing cost formula in everyday business operations.
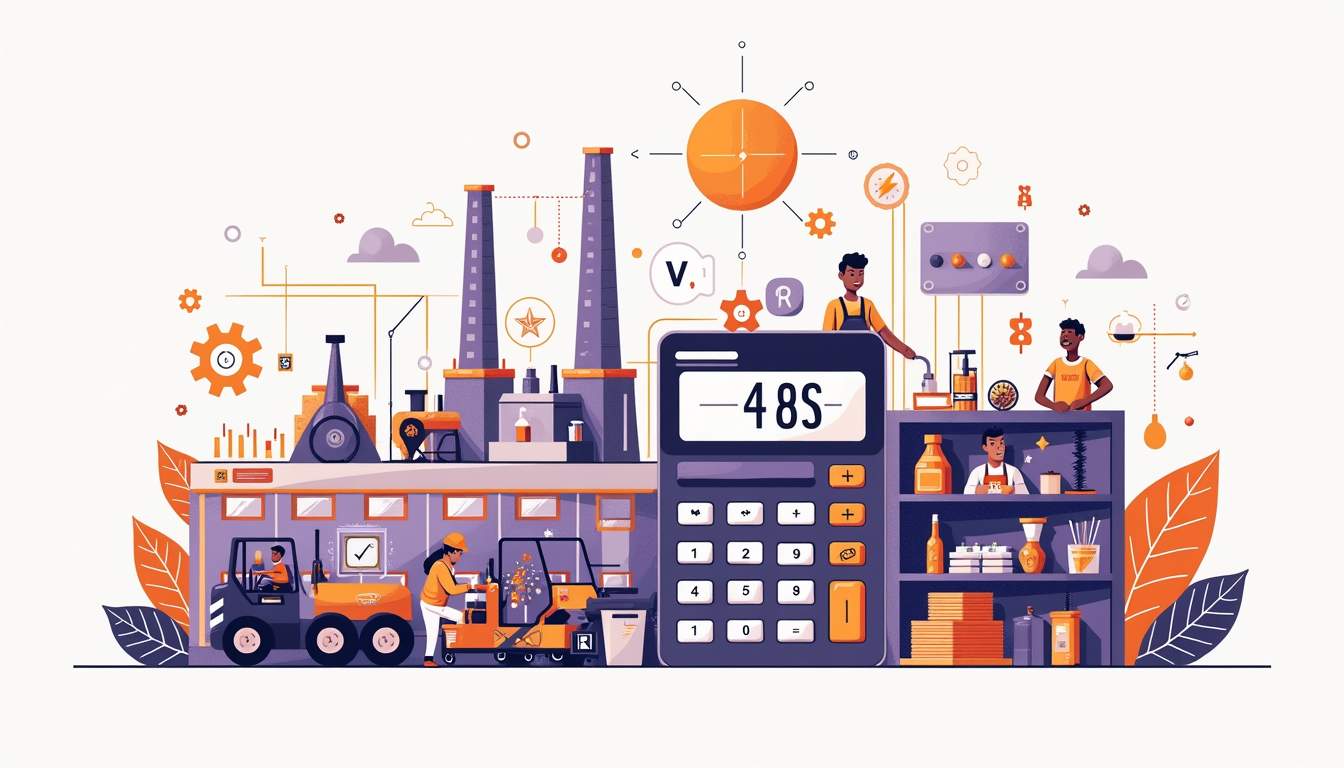
Understanding Optimum Stock Level
Maintaining an optimum stock level is a crucial aspect of managing total manufacturing cost. By understanding the trade-off between holding costs and ordering costs, businesses can better manage their inventory to minimize costs while ensuring they meet production needs.
A furniture manufacturer, for example, might analyze its sales trends to determine the ideal stock of wood and materials that balances production efficiency with cost savings. This approach not only reduces costs but also increases responsiveness to market demands. Additionally, by leveraging technology such as inventory management software, the manufacturer can forecast demand more accurately, allowing for timely adjustments in stock levels and minimizing the risks of stockouts or overstock situations.
The Role of Batch Production in Manufacturing
Batch production allows manufacturers to produce goods in groups or batches, which can be an effective strategy for controlling total costs. This method is particularly useful for products with fluctuating demand, allowing businesses to tailor production to actual sales trends.
Take a bakery for instance. Instead of producing an extensive inventory, they might use batch production to bake goods based on daily demand, reducing waste while optimizing labor and materials. Understanding batch production costs helps in applying the total manufacturing cost formula thoroughly. Furthermore, implementing a just-in-time (JIT) approach can enhance this strategy, as it encourages the bakery to procure ingredients only as needed for production, further minimizing storage costs and ensuring freshness.
Evaluating the Make to Stock Strategy: Pros and Cons
The make-to-stock strategy, where products are made based on anticipated customer demand and held in inventory, has its own set of implications for total manufacturing costs. While this strategy can lead to economies of scale, it also risks producing excess inventory that can tie up resources.
For a clothing manufacturer, transitioning to a make-to-order strategy could alleviate some of the risks associated with overproduction. However, this requires a thorough analysis of manufacturing costs in order to navigate the transition smoothly and recognize benefits. Additionally, adopting a flexible production system can allow manufacturers to pivot between make-to-stock and make-to-order as market conditions change, ensuring they remain agile and responsive to consumer preferences.
Moreover, integrating customer feedback into the production planning process can enhance the effectiveness of the make-to-stock strategy. By closely monitoring customer trends and preferences, manufacturers can adjust their production schedules and inventory levels, thereby aligning their output more closely with actual market demand and reducing the likelihood of excess inventory.