Simplifying E-Commerce Inventory with a Bill of Materials: A Step-by-Step Guide
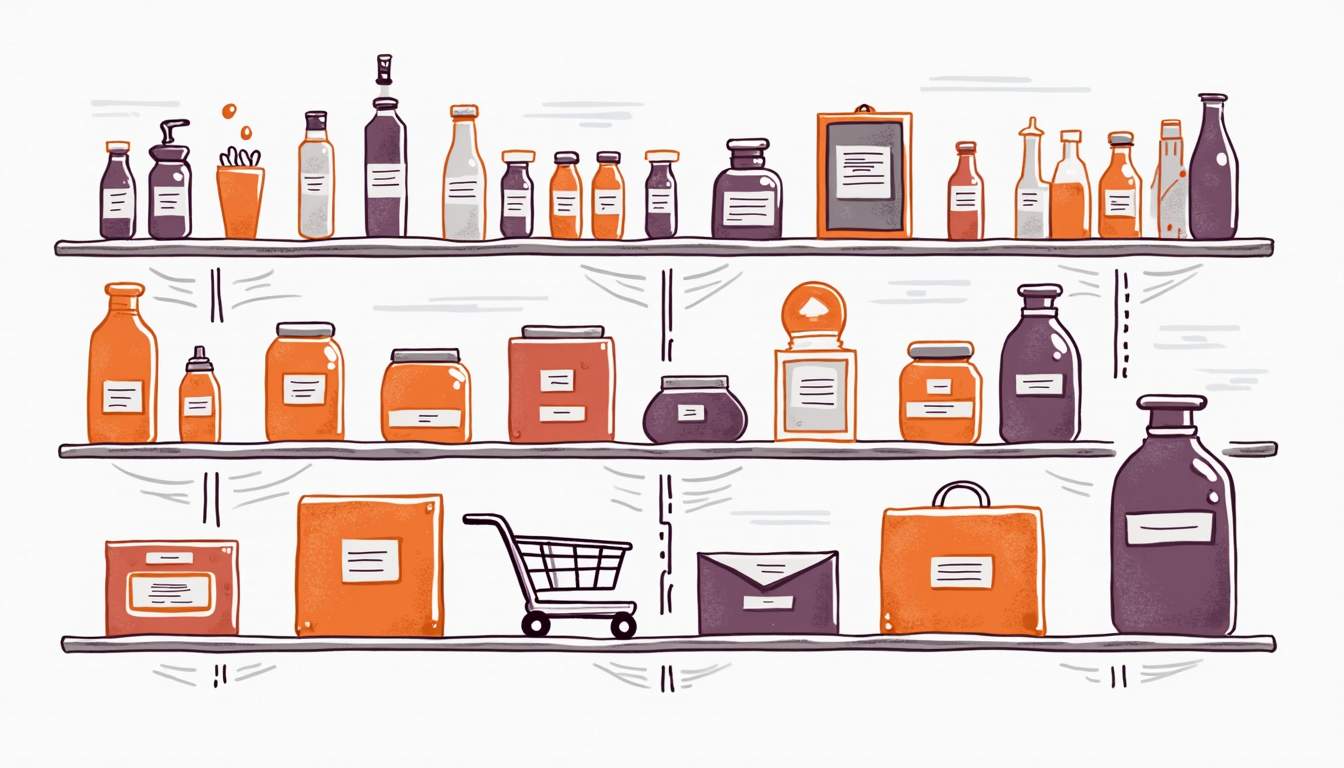
In the bustling world of e-commerce, managing inventory efficiently is crucial for success. One of the most effective tools for streamlining inventory management is the Bill of Materials (BOM). This comprehensive guide will walk you through the process of using a BOM to simplify your e-commerce inventory, ensuring that you can meet customer demands without overstocking or understocking your products.
Understanding the Bill of Materials
What is a Bill of Materials?
A Bill of Materials is a detailed list of raw materials, components, and instructions required to construct, manufacture, or repair a product or service. In the context of e-commerce, a BOM serves as a blueprint for assembling products, helping businesses track inventory levels, manage supply chains, and streamline production processes.
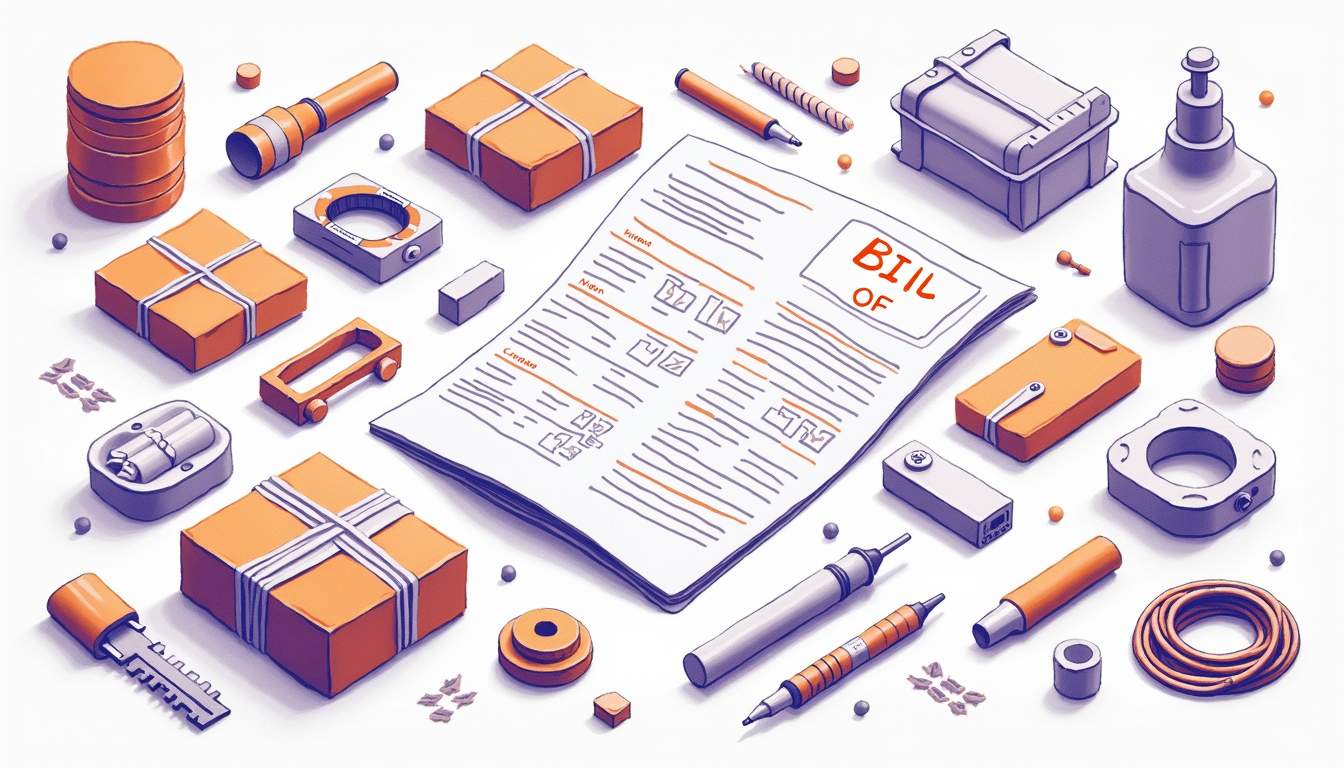
By breaking down a product into its individual components, a BOM provides a clear picture of what is needed to produce each item. This not only aids in inventory management but also helps in cost estimation and production planning. Whether you're assembling electronics, crafting handmade goods, or packaging kits, a BOM is an invaluable tool for ensuring that all necessary parts are available when needed.
Types of Bill of Materials
There are several types of BOMs, each serving a different purpose. The most common types include the Engineering BOM (EBOM), which is used during the product design phase, and the Manufacturing BOM (MBOM), which is used during the production phase. For e-commerce businesses, the MBOM is particularly useful as it outlines the components needed to manufacture a product, including packaging materials and instructions.
Another type is the Sales BOM, which is used when a product is sold as a kit or bundle. This BOM lists the finished product and its components as separate line items, allowing for easier tracking and management of bundled sales. Understanding the different types of BOMs can help businesses choose the right one for their specific needs, ensuring efficient inventory management and production processes.
Benefits of Using a Bill of Materials in E-Commerce
Improved Inventory Management
One of the primary benefits of using a BOM in e-commerce is improved inventory management. By providing a detailed list of components required for each product, a BOM helps businesses maintain optimal inventory levels. This reduces the risk of overstocking, which can lead to increased storage costs, and understocking, which can result in missed sales opportunities.
With a BOM, businesses can easily track the availability of each component, ensuring that they have enough materials on hand to meet customer demand. This not only improves inventory accuracy but also enhances the overall efficiency of the supply chain, leading to faster production times and improved customer satisfaction.
Cost Control and Budgeting
Another significant advantage of using a BOM is the ability to control costs and improve budgeting. By breaking down a product into its individual components, a BOM provides a clear picture of the cost of each part. This allows businesses to identify areas where they can reduce costs, such as by finding cheaper suppliers or optimizing production processes.
Additionally, a BOM helps businesses create more accurate budgets by providing detailed cost estimates for each product. This enables businesses to plan their finances more effectively, ensuring that they have the resources needed to meet production demands without overspending. By improving cost control and budgeting, a BOM can help businesses increase profitability and achieve long-term success.
Creating a Bill of Materials: A Step-by-Step Guide
Step 1: Identify the Product Structure
The first step in creating a BOM is to identify the structure of the product. This involves breaking down the product into its individual components and sub-components. Start by listing the main components of the product, then identify any sub-components that are needed to assemble each main component. This hierarchical structure will serve as the foundation for your BOM.
When identifying the product structure, consider the assembly process and any dependencies between components. For example, if a component cannot be assembled until another component is complete, make note of this in your BOM. This will help ensure that your production process runs smoothly and efficiently.
Step 2: List All Components and Materials
Once you have identified the product structure, the next step is to list all the components and materials needed to assemble the product. This includes raw materials, purchased parts, and any other items required for production. Be sure to include detailed descriptions of each component, including part numbers, quantities, and specifications.
In addition to listing the components, consider including information about suppliers and lead times. This will help you manage your supply chain more effectively, ensuring that you have the materials you need when you need them. By providing a comprehensive list of components and materials, your BOM will serve as a valuable resource for inventory management and production planning.
Step 3: Define the Assembly Process
After listing all the components and materials, the next step is to define the assembly process. This involves outlining the steps required to assemble the product, including any special instructions or precautions. Consider including diagrams or illustrations to help clarify the assembly process and ensure that it is easy to follow.
By clearly defining the assembly process, you can help ensure that your production team has the information they need to assemble the product efficiently and accurately. This not only improves the quality of the finished product but also reduces the risk of errors and rework, leading to cost savings and improved customer satisfaction.
Integrating a Bill of Materials with Inventory Management Systems
Choosing the Right Inventory Management Software
Integrating a BOM with your inventory management system can further streamline your e-commerce operations. To do this effectively, it's important to choose the right inventory management software. Look for software that supports BOM integration and offers features such as real-time inventory tracking, automated reordering, and reporting capabilities.
Consider the size and complexity of your business when selecting inventory management software. Smaller businesses may benefit from simple, user-friendly solutions, while larger businesses may require more advanced software with additional features and customization options. By choosing the right software, you can ensure that your BOM is seamlessly integrated into your inventory management processes.
Automating Inventory Updates
Once you have chosen the right inventory management software, the next step is to automate inventory updates. This involves setting up your software to automatically update inventory levels based on the information in your BOM. For example, when a product is assembled, the software should automatically deduct the components used from your inventory.
By automating inventory updates, you can reduce the risk of errors and ensure that your inventory levels are always accurate. This not only improves inventory management but also enhances the efficiency of your supply chain, leading to faster production times and improved customer satisfaction.
Monitoring and Adjusting Your BOM
Finally, it's important to regularly monitor and adjust your BOM to ensure that it remains accurate and up-to-date. This involves reviewing your BOM periodically to identify any changes in component availability, costs, or specifications. If any changes are identified, be sure to update your BOM accordingly.
By regularly monitoring and adjusting your BOM, you can ensure that it continues to serve as an effective tool for inventory management and production planning. This not only helps you meet customer demand but also improves the overall efficiency and profitability of your e-commerce business.
Conclusion
Implementing a Bill of Materials in your e-commerce operations can significantly simplify inventory management and enhance your production processes. By understanding the structure and components of a BOM, and integrating it with your inventory management systems, you can achieve greater efficiency, cost control, and customer satisfaction. As you continue to refine your BOM and adapt to changes in the market, you'll be well-equipped to meet the demands of your customers and drive your business towards success.
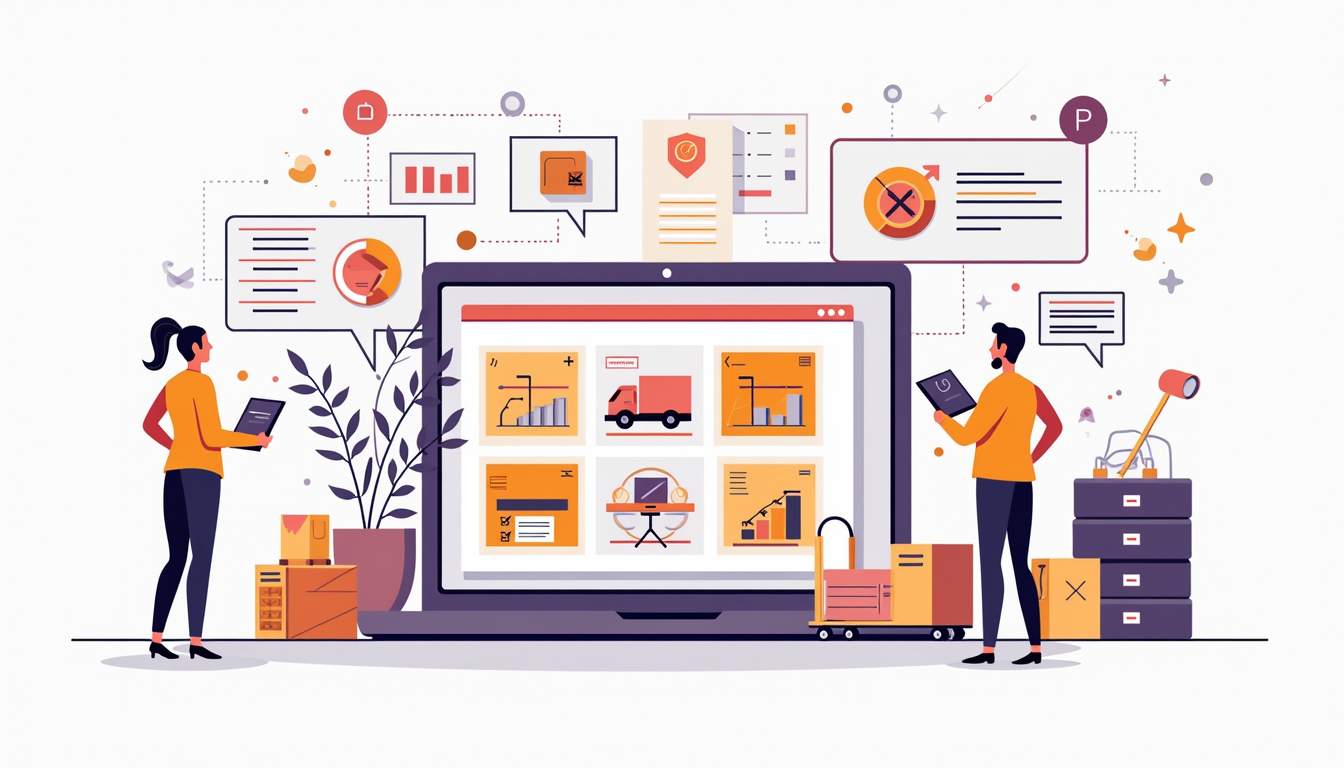