Understanding the Benefits of Batch Production in Manufacturing
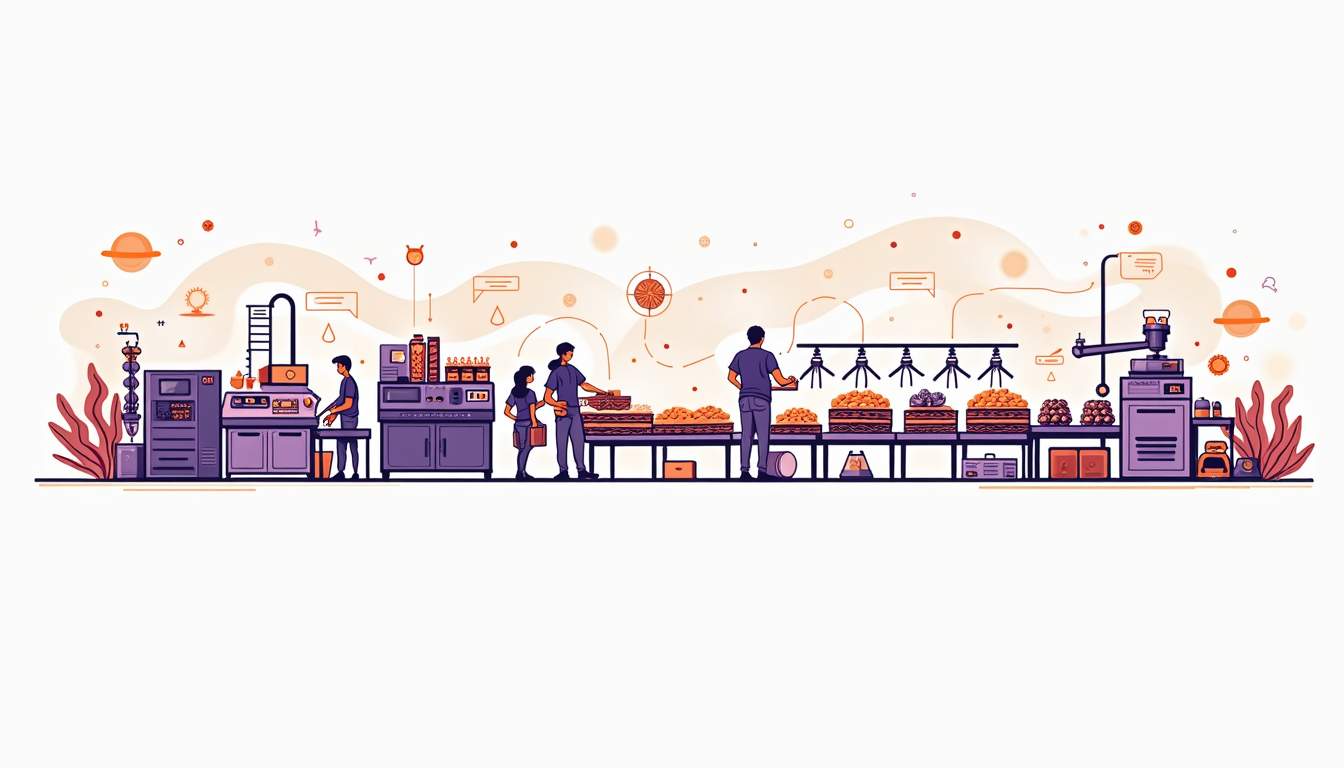
Batch production is a manufacturing technique that involves producing goods in groups or batches rather than in a continuous stream. This approach can be highly beneficial for various industries, offering flexibility and efficiency. In this article, we will explore the rationale behind batch production, real-world examples, its pros and cons, and how it ties into inventory management.
The Rationale Behind Batch Production in Manufacturing
At its core, batch production allows manufacturers to produce multiple items simultaneously, which can lead to significant cost savings and increased efficiency. Instead of setting up equipment for a single item, batching allows for the production of several units in one go. This can particularly benefit industries like food production, textiles, and consumer goods.
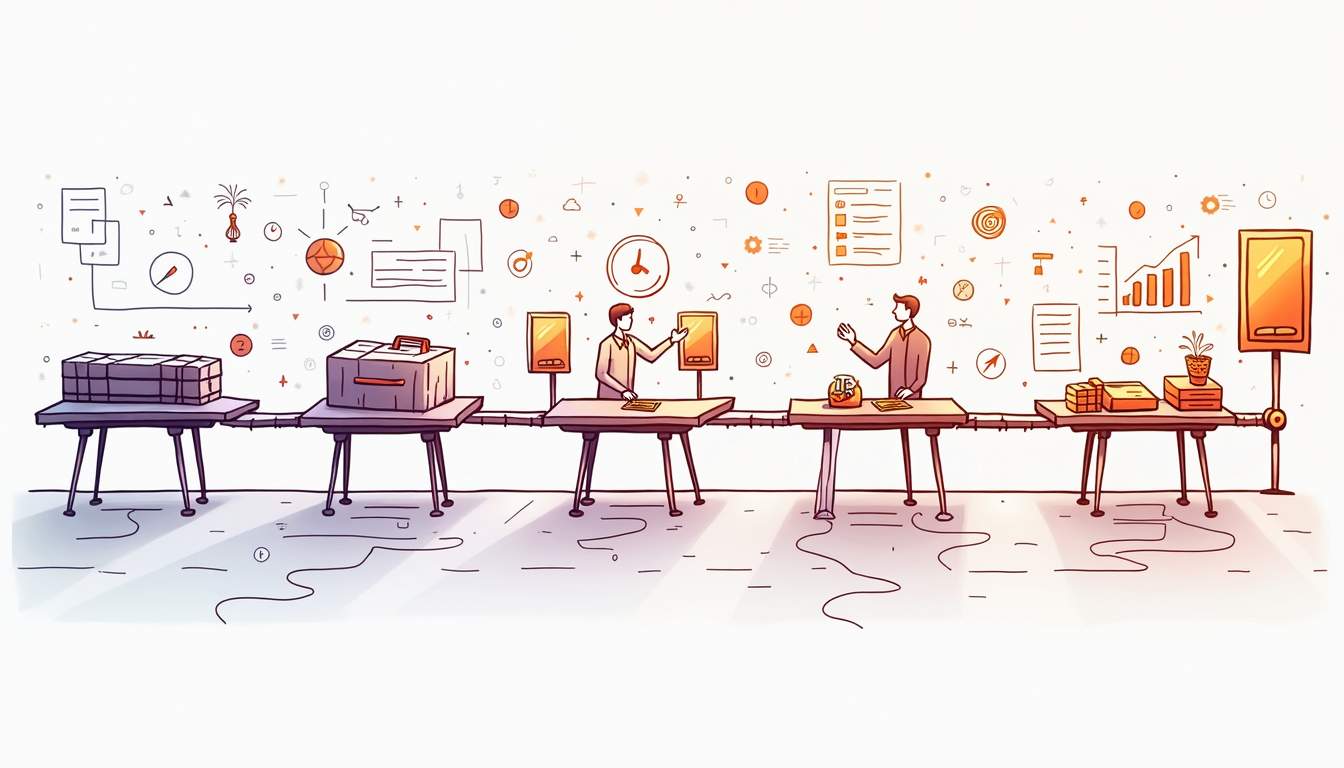
In batch production, companies can respond more easily to changes in consumer demand. For instance, if a particular product sees a surge in popularity, a manufacturer can quickly ramp up production by increasing the size of the batch rather than overhauling an entire production line.
Moreover, this method minimizes waste by allowing manufacturers to use raw materials more efficiently. It also enables businesses to conduct maintenance on their machinery between batches, thereby reducing downtime and keeping operations running smoothly.
Additionally, batch production can enhance product quality through controlled processes. By producing items in groups, manufacturers can implement quality checks at various stages of production, ensuring that any defects are caught early and rectified before the entire batch is completed. This systematic approach not only improves the final product but also builds consumer trust, as customers are more likely to receive consistent quality with each purchase.
Another significant advantage of batch production is its flexibility. Manufacturers can easily switch between different products or variations within the same production run. This adaptability is essential in industries where trends change rapidly, allowing companies to innovate and introduce new products without the need for extensive reconfiguration of their production lines. As a result, businesses can maintain a competitive edge by being agile and responsive to market demands, which is increasingly crucial in today's fast-paced economy.
Understanding Batch Production Through Real-World Examples
To grasp the advantages of batch production, let's look at some real-world applications. A prime example can be seen in the bakery industry. Bakeries often produce items like bread, pastries, and cakes in batches. For instance, a bakery might choose to make 100 loaves of bread at once instead of baking each loaf individually. This method lowers production costs, saves time, and enables the bakery to meet higher demand during peak hours. Additionally, batch production allows bakers to optimize their use of ovens and other equipment, ensuring that energy consumption is minimized while maximizing output. By producing in larger quantities, bakers can also experiment with different recipes and flavors, creating seasonal specialties that attract customers and keep the menu fresh and exciting.
Another example is in the textile industry. Companies may produce clothing lines in specific batches. When a new fashion season approaches, brands create batches of shirts, dresses, and accessories that reflect the latest trends. This strategy allows them to remain relevant while minimizing the resources spent on outdated designs. Furthermore, batch production in textiles enables manufacturers to streamline their supply chain processes. By coordinating the production of various items, they can reduce lead times and ensure that retailers receive their stock in a timely manner, which is crucial for capitalizing on fleeting fashion trends. The ability to quickly pivot and adjust batch sizes based on consumer feedback also enhances responsiveness, allowing brands to make data-driven decisions that align with market demands.
These examples illustrate how batch production isn't just theoretical; it’s a practical approach that can enhance productivity and meet market demand effectively. By leveraging batch production techniques, industries can not only improve efficiency but also foster innovation and creativity in their product offerings, ultimately leading to a more dynamic and competitive marketplace.
Pros and Cons of Batch Production
Like any production method, batch production comes with its own set of advantages and disadvantages. Understanding these can help businesses make informed decisions.
Benefits of Implementing Batch Production
One of the most notable benefits of batch production is efficiency. By producing several items at once, manufacturers can save on setup times and reduce labor costs. In addition, batch production allows for streamlined processes, as workers can focus on specific tasks during each production cycle, increasing overall productivity.
Quality control is another advantage. Since batch production can facilitate more focused oversight, manufacturers can ensure consistency in the products being made. This is particularly important in industries where imperfections can result in a significant loss of quality, such as pharmaceuticals or food production. Moreover, the ability to conduct quality checks between batches allows for immediate rectification of any issues, which can enhance the overall reliability of the production process.
Flexibility is also key. Companies can easily adapt their production strategies based on current market demands, transitioning quickly from one batch to another as needed. This responsiveness can lead to better customer satisfaction and loyalty. For example, a clothing manufacturer can shift from producing winter apparel to summer collections with relative ease, allowing them to capitalize on seasonal trends without extensive downtime.
Another significant benefit is the potential for innovation. Batch production allows companies to experiment with new products or variations without committing to a full-scale production run. This can be particularly advantageous for businesses looking to test new ideas in the market, gather feedback, and refine their offerings before a larger launch.
Drawbacks of Batch Production
Conversely, batch production does have its drawbacks. One significant concern is inventory management. Keeping large quantities of raw materials on hand may be necessary, which can tie up company funds and space. If products become obsolete or demand decreases unexpectedly, companies may face significant losses due to excess inventory. This challenge is compounded by the need for accurate forecasting, which can be difficult in rapidly changing markets.
Additionally, the setup time for each batch can lead to inefficiencies in some cases, especially if the batches are small and the changeover process is lengthy. This can negate some of the efficiencies gained through batch production. Furthermore, if production schedules are not meticulously planned, delays in one batch can cascade into subsequent batches, causing a ripple effect that disrupts the entire production timeline.
Finally, if not managed carefully, batch production can lead to a lack of variety in the product line, which may alienate customers seeking novelty and diversity. Over time, a company may find itself pigeonholed into producing only a few variations of a product, losing out on opportunities to attract new customers or retain existing ones who crave fresh options. This stagnation can be detrimental in competitive markets where consumer preferences are constantly evolving.
Defining Optimum Stock Levels in Inventory Management
In any production environment, especially in batch production, determining the right stock levels is crucial. This balance ensures that manufacturers have enough materials to meet production needs without overextending their resources. The challenge lies in accurately predicting the amount of stock required, as fluctuations in demand can lead to either shortages or excess inventory, both of which can be detrimental to a business's bottom line.
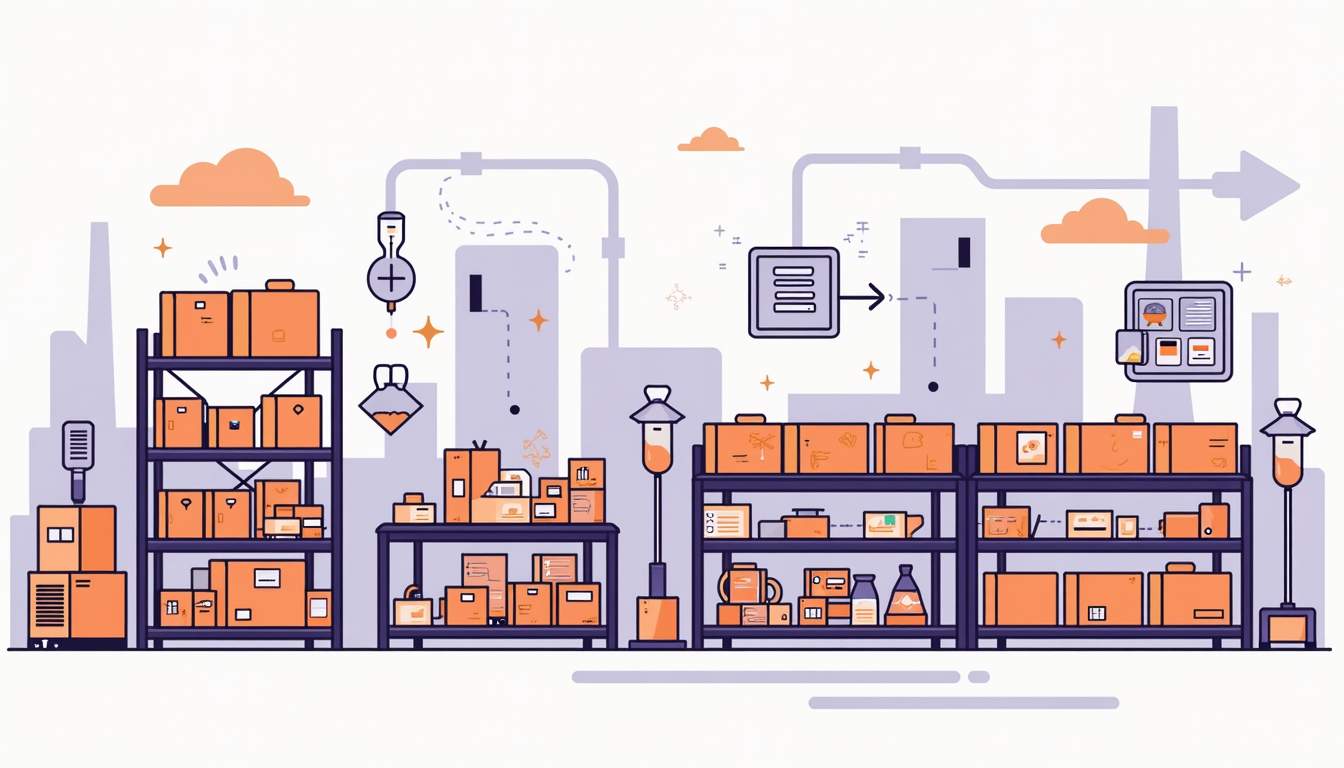
Optimum stock levels can help minimize storage costs while still allowing businesses to respond to market demands quickly. Striking this balance often requires sophisticated forecasting and demand planning strategies to project future needs accurately. Advanced technologies, such as artificial intelligence and machine learning, are increasingly being integrated into inventory management systems to analyze historical sales data and predict future trends, enabling companies to make more informed decisions regarding their stock levels.
Make to Stock Strategy: Benefits and Limitations
The make to stock (MTS) strategy is commonly employed in conjunction with batch production. In this model, products are manufactured based on forecasted demand and stored until ordered. This strategy can lead to quick fulfillment times when demand arises, which is an advantage for manufacturers. For instance, industries such as consumer electronics or fast-moving consumer goods benefit significantly from MTS, as they can ensure that popular products are readily available to meet consumer needs without delay.
However, the limitations of this strategy must also be acknowledged. If forecasts are inaccurate, companies may face overproduction, resulting in excessive inventory that cannot be sold. This not only ties up financial resources but can also lead to waste if products perish or become outdated. Moreover, holding large amounts of inventory can increase storage costs and complicate warehouse management, leading to inefficiencies. Therefore, successful implementation of MTS requires a keen understanding of market trends and customer preferences, further emphasizing the need for robust inventory management. Regularly revisiting and adjusting forecasting methods, alongside maintaining open lines of communication with sales and marketing teams, can help mitigate some of these risks and enhance the overall effectiveness of the MTS strategy.
An Overview of Inventory Control
Efficient inventory control is essential for successful batch production and optimum stock level management. Inventory control enables businesses to track and manage their stock levels, order fulfillment, and storage costs. This process not only aids in maintaining the right amount of inventory but also plays a significant role in enhancing customer satisfaction by ensuring that products are available when needed.
Effective inventory control methods can lead to a streamlined production process. By having clear visibility into stock levels, manufacturers can avoid delays due to shortages or overstock situations. Moreover, an organized inventory system can significantly reduce waste, as it helps in identifying slow-moving items that may need to be discounted or bundled with other products to encourage sales.
Key Methods of Inventory Management
Several key methods of inventory management can improve batch production efficiency. Just-in-time (JIT) inventory management is one such method, aiming to reduce storage costs by receiving goods only as they are needed in the production process. This approach not only minimizes holding costs but also encourages a more agile response to market demands, allowing manufacturers to adapt quickly to changes in consumer preferences.
Another method is the use of inventory management software, which can provide real-time data on stock levels, demand forecasts, and order statuses, helping businesses make informed decisions. These software solutions often come equipped with advanced analytics tools that can predict trends and provide insights into customer behavior, enabling businesses to optimize their inventory strategies further.
Additionally, maintaining accurate records, conducting regular audits, and employing barcoding systems can enhance inventory tracking, ensuring that businesses are always prepared to meet production demands. Implementing these systems not only improves accuracy but also fosters a culture of accountability within the organization, as employees become more aware of the importance of precise inventory management.
Getting Started with Inventory Control Basics
For manufacturers looking to improve their inventory management practices, starting with the basics is essential. First, businesses need to establish clear inventory goals and understand their unique production needs. This foundational step involves analyzing historical sales data and current market trends to set realistic targets that align with overall business objectives.
Next, selecting the right inventory management system that aligns with these goals is crucial. Training staff to use these systems effectively will also promote efficiency and accuracy in data handling. Furthermore, fostering a collaborative environment where employees can share insights and feedback on inventory processes can lead to continuous improvement and innovation in inventory control practices.
Finally, regularly reviewing and adjusting inventory strategies is vital to ensure that they remain relevant and effective in an ever-changing market landscape. This ongoing assessment may include exploring new technologies, such as artificial intelligence and machine learning, which can provide deeper insights into inventory trends and automate routine tasks, freeing up valuable time for staff to focus on strategic initiatives.
In conclusion, batch production offers numerous advantages for manufacturers looking to enhance efficiency and adaptability. By understanding this method through real-world examples, weighing its pros and cons, and effectively managing inventory, businesses can thrive in a competitive landscape. Cultivating a strong grasp of these principles will pave the way for long-term success and customer satisfaction.