Using a Bill of Materials to Improve Product Assembly and Inventory Efficiency in E-Commerce
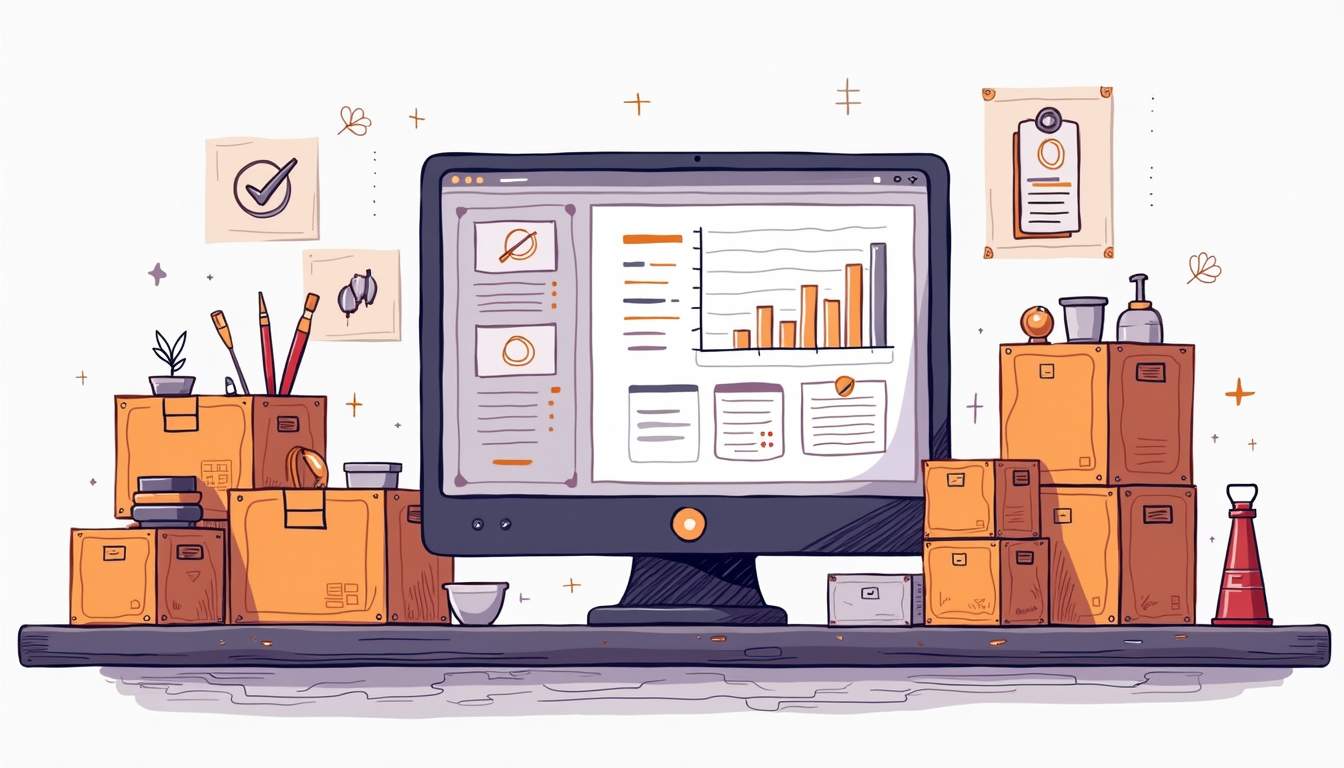
In the rapidly evolving world of e-commerce, efficiency is the name of the game. As businesses strive to meet increasing consumer demands, the need for streamlined operations becomes paramount. A Bill of Materials (BOM) is a critical tool that can significantly enhance product assembly and inventory management, leading to improved efficiency and profitability. By understanding and implementing a BOM, e-commerce businesses can optimize their production processes, reduce waste, and ensure timely delivery of products to customers.
Understanding the Bill of Materials
What is a Bill of Materials?
A Bill of Materials is a comprehensive list of raw materials, components, and assemblies required to construct, manufacture, or repair a product. It serves as a blueprint for the production process, detailing every item needed and the quantity required. In e-commerce, a BOM is essential for managing inventory and ensuring that all parts are available for timely product assembly.
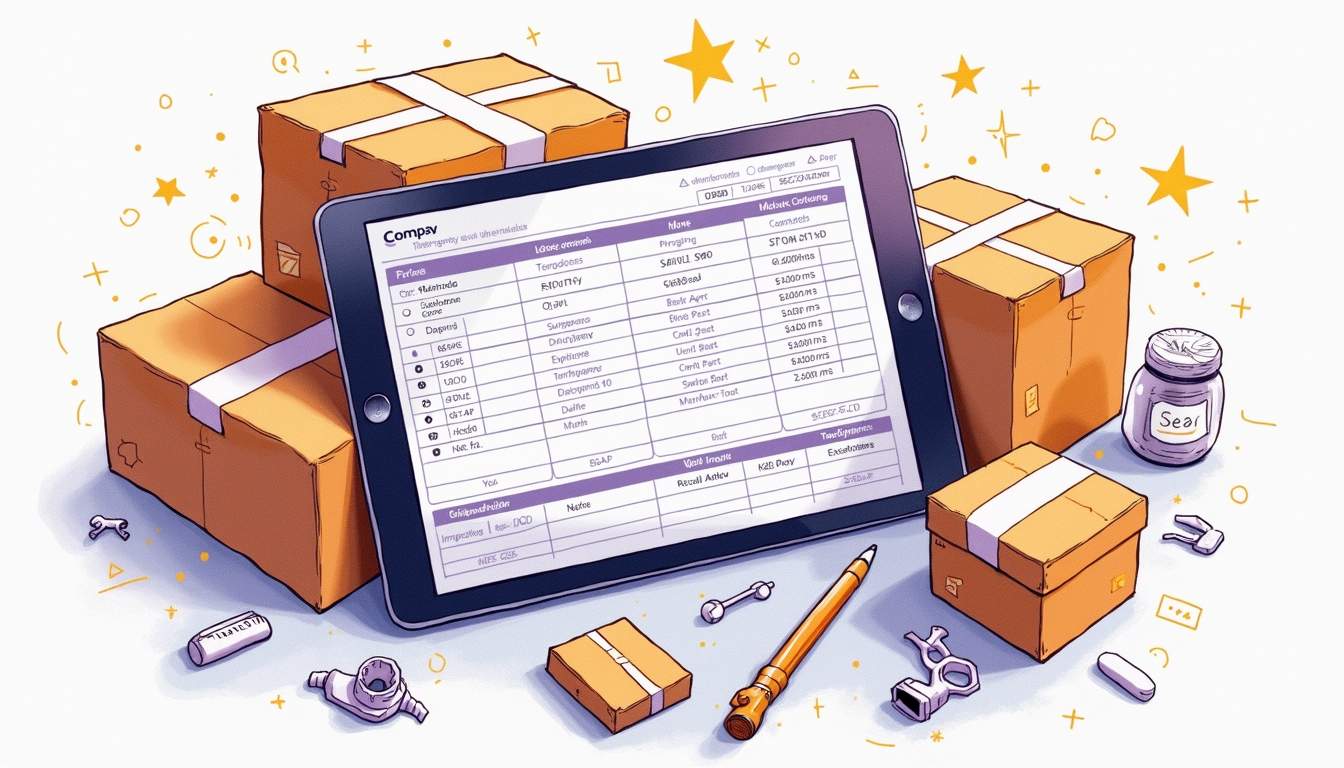
The BOM is often referred to as the "recipe" for a product, as it outlines the precise ingredients and steps necessary to create the final product. This document is crucial for manufacturers, suppliers, and inventory managers, as it provides a clear and organized framework for production.
Types of Bill of Materials
There are several types of BOMs, each serving a specific purpose. The most common types include the Engineering BOM (EBOM), Manufacturing BOM (MBOM), and Sales BOM (SBOM). The EBOM is used during the product design phase and includes technical specifications. The MBOM is utilized in the manufacturing process, detailing the components needed for production. The SBOM is used in sales and customer service, outlining the finished product and its components.
Understanding the different types of BOMs is crucial for e-commerce businesses, as it allows them to tailor their inventory and production processes to meet specific needs. By selecting the appropriate BOM type, companies can ensure that their operations are aligned with their business goals.
Benefits of Using a Bill of Materials in E-Commerce
Improved Inventory Management
One of the primary benefits of using a BOM in e-commerce is improved inventory management. By providing a detailed list of all components needed for product assembly, a BOM helps businesses maintain optimal inventory levels. This ensures that all necessary materials are on hand when needed, reducing the risk of production delays and stockouts.
With a BOM, businesses can also track inventory usage and identify trends in material consumption. This information can be used to forecast future inventory needs, allowing companies to make informed purchasing decisions and avoid overstocking or understocking.
Enhanced Product Assembly Efficiency
A BOM streamlines the product assembly process by providing a clear and organized framework for production. By detailing the specific components and quantities required, a BOM eliminates guesswork and reduces the likelihood of errors during assembly. This leads to faster production times and improved product quality.
Additionally, a BOM can help identify potential bottlenecks in the assembly process, allowing businesses to address these issues proactively. By optimizing the assembly process, companies can increase production capacity and meet customer demands more effectively.
Cost Savings and Waste Reduction
Using a BOM can lead to significant cost savings by minimizing waste and reducing the need for excess inventory. By accurately forecasting material requirements, businesses can avoid over-purchasing and reduce storage costs. This not only lowers operational expenses but also contributes to a more sustainable business model.
Furthermore, a BOM can help identify opportunities for cost savings through material substitutions or process improvements. By analyzing the BOM, businesses can explore alternative materials or methods that may be more cost-effective, without compromising product quality.
Implementing a Bill of Materials in Your E-Commerce Business
Steps to Create a Bill of Materials
- Identify the Product Structure: Begin by outlining the product structure, including all components, sub-assemblies, and raw materials required. This will serve as the foundation for your BOM.
- List All Components: Create a detailed list of all components, including part numbers, descriptions, and quantities. Be sure to include any additional information that may be relevant, such as supplier details or lead times.
- Organize the BOM Hierarchically: Arrange the BOM in a hierarchical format, with the finished product at the top and individual components listed below. This will provide a clear visual representation of the product structure.
- Review and Validate: Once the BOM is complete, review it for accuracy and completeness. Validate the information with relevant stakeholders, such as engineers or suppliers, to ensure that all components are accounted for.
Integrating BOM with Inventory Management Systems
To maximize the benefits of a BOM, it is essential to integrate it with your inventory management system. This integration allows for real-time tracking of inventory levels and ensures that all components are available when needed. By linking the BOM to your inventory system, you can automate reordering processes and reduce the risk of stockouts.
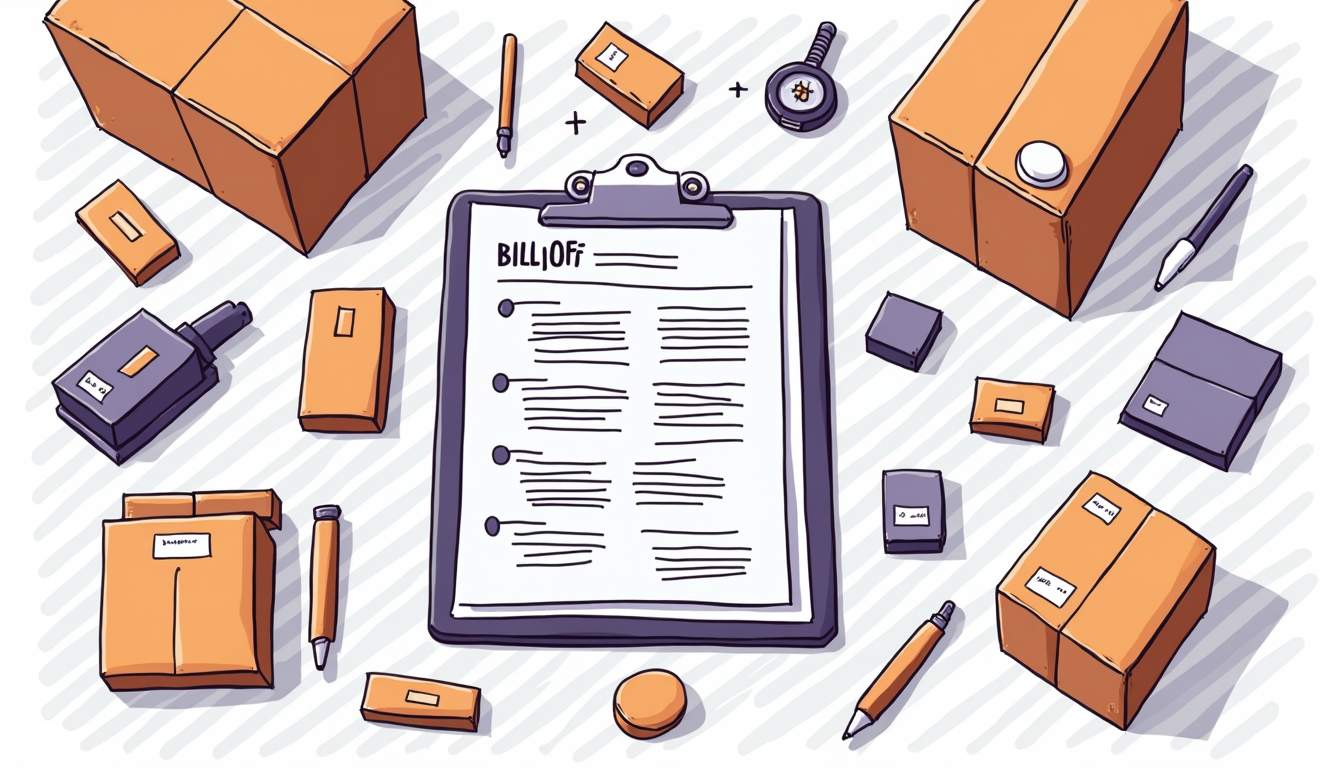
Many e-commerce businesses use software solutions that offer BOM management features, allowing for seamless integration with existing inventory systems. These tools can help streamline operations, improve data accuracy, and enhance overall efficiency.
Challenges and Considerations
Maintaining BOM Accuracy
One of the primary challenges of using a BOM is maintaining its accuracy over time. As products evolve and new components are introduced, the BOM must be updated to reflect these changes. Regular reviews and updates are essential to ensure that the BOM remains a reliable source of information.
Inaccurate BOMs can lead to production delays, increased costs, and customer dissatisfaction. To mitigate these risks, businesses should establish processes for regularly reviewing and updating their BOMs, involving key stakeholders in the process.
Managing Complex Product Structures
For businesses with complex product structures, managing a BOM can be challenging. Products with multiple sub-assemblies or variants require detailed and comprehensive BOMs, which can be time-consuming to create and maintain. However, investing in robust BOM management tools can simplify this process and ensure that all components are accurately documented.
Additionally, businesses should consider implementing standardized naming conventions and part numbering systems to facilitate easier management of complex BOMs. This can help reduce errors and improve communication among team members.
Conclusion
In the competitive landscape of e-commerce, leveraging a Bill of Materials can significantly enhance product assembly and inventory efficiency. By providing a detailed blueprint for production, a BOM helps businesses optimize their operations, reduce costs, and improve customer satisfaction. While challenges exist, the benefits of implementing a BOM far outweigh the potential drawbacks. By understanding and utilizing this powerful tool, e-commerce businesses can position themselves for long-term success and growth.